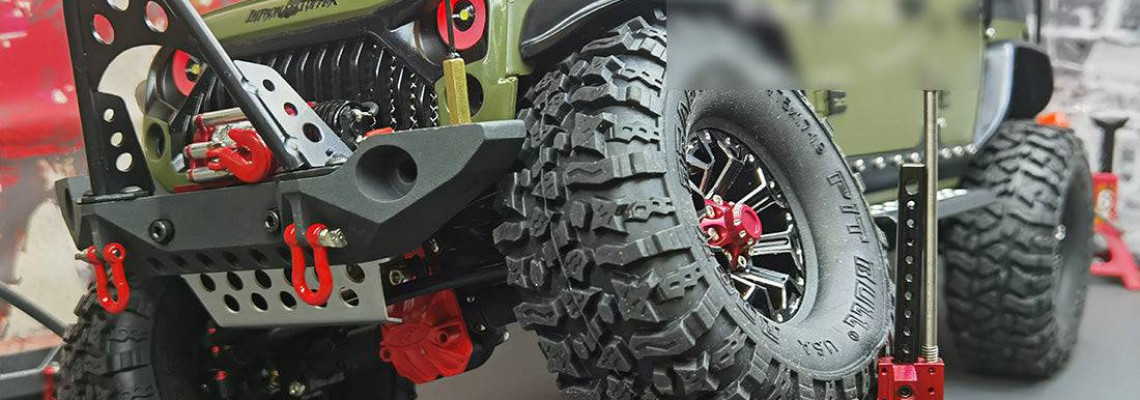
ESC - Electronic Speed Controllers and understanding them
What is an electronic speed controller?
Electronic speed controller. As is well known, an ESC regulates the aeroplane's motor spin speed. It serves a function similar to a glow-powered aeroplane's throttle servo. It is an advantage between the power plant and an aeroplane's radio receiver. Three wire sets make up an electrical speed control.
What does ESC stand for?
An electronic circuit that regulates and controls an electric motor's speed is called an electronic speed control (ESC). It might also include dynamic braking and motor reversing. Electrically powered radio-controlled models use miniature electronic speed controllers, and full-size electric cars are equipped with speed control systems.
Function
An electronic speed control modifies the switching rate of a network of field effect transistors (FETs) in response to a speed reference signal obtained from a throttle lever, joystick, or other physical input.[1] The motor's speed can be altered by varying the transistors' duty cycle or switching frequency. The motor's distinctive high-pitched whine, particularly audible at lower speeds, is caused by the quick changes in the current passing through it.
Brushless DC motors and brushed DC motors require different kinds of speed controls. Brushless motors have a different operating principle, and motors with electromagnet field windings instead of permanent magnets can also have their speed controlled by adjusting the strength of the motor field current. Brushless motors work by varying the timing of current pulses delivered to the motor's multiple windings.
A generic ESC module with an integrated eliminator circuit and a 35-ampere rating
Like a variable frequency drive, brushless ESC systems generate three-phase AC electricity to power brushless motors. Compared to conventional brushed motors, brushless motors are more efficient, powerful, long-lasting, and lightweight, which makes them popular among radio-controlled aviation enthusiasts. Compared to brushed motor controllers, brushless DC motor controllers are far more complex.[2]
The ESC must account for the proper phase of the current supplied to the motor changing as the motor rotates. The back EMF often detects this rotation from the motor windings, but some variants employ optical detectors or independent magnetic (Hall effect) sensors. Computer-programmable speed controls often offer user-specified settings for low voltage cut-off limits, timing, acceleration, braking, and rotational direction. Any two of the three lines from the ESC to the motor can also be switched to reverse the direction of the motor.
Classification
When choosing a battery eliminator circuit (BEC), whether integrated into the controller or as a standalone unit, the type of battery and number of cells connected are essential considerations; a higher number of cells connected will result in a reduced power rating and, therefore, a lower number of servos supported by an integrated BEC, if it uses a linear voltage regulator; a well-designed BEC using a switching regulator should not have a similar limitation. ESCs are typically rated according to maximum current, such as 25 amperes (25 A).
ESC firmware
Most current ESCs feature a microcontroller that analyzes the input signal and suitably operates the motor using a built-in program or firmware. In some circumstances, updating the factory's built-in firmware for another publicly available open-source firmware is feasible. This is generally done to adjust the ESC to a given application. Some ESCs are factory-equipped with the potential of user upgradable software. Others require soldering to connect a programmer. ESCs are generally marketed as black boxes with proprietary firmware. In 2014, a Swedish developer named Benjamin Vedder started an open-source ESC project eventually called VESC.[3] The VESC project has subsequently received attention for its advanced customization options and relatively low build price compared to other high-quality ESCs.[4]
Remote control applications
As is the case with tIn most toy-grade R/C vehicles, an ESC can be integrated into the receiver or be a standalone device that connects to the receiver's throttle control channel. Certain R/C manufacturers use onboard electronics that integrate proprietary hobby-grade electronics on a single circuit board in entry-level cars, boats, or aeroplanes.
Electronic speed controls for model RC vehicles may include a battery eliminator circuit to adjust receiver voltage to eliminate the need for separate receiver batteries. The mode of the regulator can be either switching or linear. In a broader context, ESCs are electric motor PWM controllers. The ESC often accepts a nominal 50 Hz PWM servo input signal with a pulse width ranging from 1 to 2 ms. The ESC reacts by shutting off the motor connected to its output when it receives a pulse with a width of 1 ms at 50 Hz. An input signal with a pulse width of 1.5 ms drives the motor at around half speed. The motor operates at full speed when an input signal of 2.0 ms is given.
Cars
Reversing is typically a feature of ESCs made for sport use in automobiles; however, more recent sports controls allow the reversing feature to be disabled, making them inoperable during a race. Dynamic braking is an extra benefit of controls, especially for racing and sports controls. The ESC compels the motor to function as a generator by applying an electrical load across the armature. Consequently, the model slows down or stops because it becomes more challenging to turn the armature. Some controllers add the advantage of regenerative braking.
Helicopters
Drone
ESCs for radio-control helicopters don't need reverse direction (which can be helpful because the motor cables can be hard to reach and replace once fitted) or braking (because the one-way bearing would make it useless).
The "governor mode" offered by many high-end helicopter ESCs locks the motor RPM at a predetermined speed, significantly facilitating CCPM-based flight. Quadcopters also make use of it.
Airplanes
Radio-control aeroplane ESCs often have a few safety measures. If the battery's power is not enough to keep the electric motor running, the ESC will reduce or turn off power to the electric motor while letting the rudder, elevator, and ailerons continue operating. This enables the pilot to maintain control of the aircraft so that it can glide or fly safely on minimal power.
Boats
Boat-specific ESCs are inherently watertight. With a denser air-trapping cage, the waterproof structure differs significantly from non-marine-type ESCs. To avoid premature failure, it becomes necessary to efficiently cool the motor and ESC. Most marine-grade ESCs are cooled by either a negative propeller vacuum close to the drive shaft output or circulated water powered by the motor. Boat ESCs can brake and reverse, the same as automobile ESCs.
Quadcopters
Modern quadcopters (and all multirotors) require Electronic Speed Controllers (ESCs), which provide a motor with high power, high frequency, and high-resolution three-phase AC electricity in a tiny package. The propeller motors' changing speed is the only power source for these ships. Fine speed control over a range of motor/prop speeds provides all the control required for a quadcopter (and all multirotors) to fly.
In contrast to the typical 50 Hz signal used in most other RC applications, quadcopter ESCs typically have a faster update rate. Modern multirotors use a range of ESC protocols, such as Oneshot42, Oneshot125, Multishot, and DShot, in addition to PWM. A digital protocol called DShot has some benefits over traditional analogue control, including excellent resolution, CRC checksums, and no oscillator drift, eliminating the need for calibration. With a DSHOT2400 frame taking only 6.5 μs, modern ESC protocols can communicate at speeds of 37.5 kHz or more.
Model trains
The electronic speed control does not need to be on board because most electric model trains are powered by energy that is either carried by the rails or by an overhead wire to the vehicle. However, this is not the case for model trains with digital steering systems, enabling several trains to operate simultaneously at varying speeds on the same track.