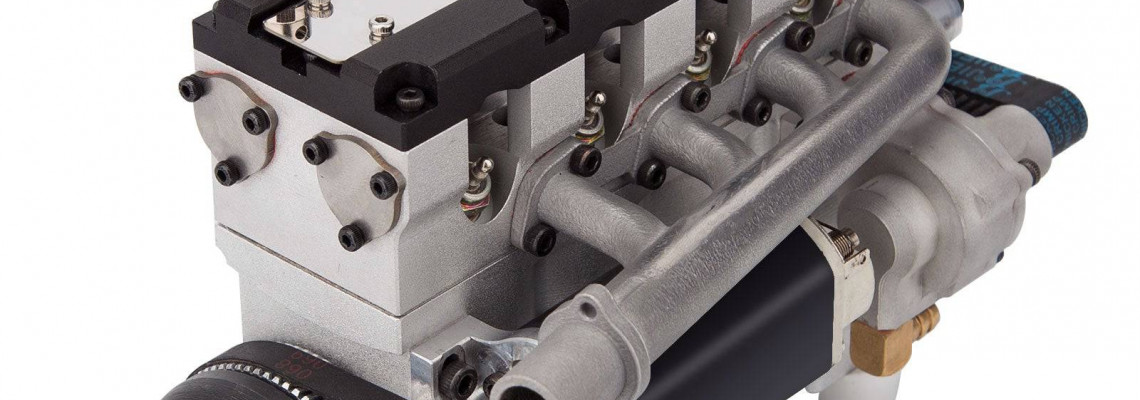
The Ultimate Guide to Assembling & Installing the Howin L6-210 Inline Engine
The processes listed below are improved when combined with the initial factory assembly process. Every stage verifies that the parts are still operating without hiccups following installation.
Put the crankshaft into the cylinder block with the camshaft bearing on your right and the smooth end of the power output facing you.
Assemble the split-type bronze bearings (numbered 51 and 52) at the crankshaft center. The steel pin (03), cap bolt (04), and main bearing cap (60) are the locations of the split-type bronze bushing.
To make sure the bearing cap (06) is installed correctly in the crankcase, first use your hands to screw in the two cap bolts (04). This is important because there may be some machine tolerance with split-type bronze bearings. Next, make sure the bearing is in the right place inside the bearing cap. You can do this by gently tapping the crankshaft ends with a small rubber mallet.
Lastly, tighten the two nuts on the cap (04). Proper installation should allow the crankshaft to spin freely.
As per step (2), install the split-type bronze bearings divergingly from the center. After a bearing is fitted correctly, the crankshaft should continue rotating freely.
After you install five sets of split-type bronze bearings, add a few drops of regular engine oil to each bearing. Use oil like 30W-40. The smoothness should be felt instantly, albeit slightly viscous.
Place the 49-inch camshaft inside the cylinder block. The cross-pin hole and the crankshaft cross-pin hole should be on the same side.
Apply a small amount of engine oil to the surfaces of both shaft ends, and then attach the e-locking ring (19), flange bearing (57), and oil seal (26). Carry out the procedure on both ends.
Install the gasket (44), oil seal (63), flywheel housing (64), screw plug (05), drain nipple (01), nipple gasket (02), and crankshaft rear ball bearing (56). Secure the flywheel housing with cap bolts (07).
Using lubricant to help it stick, place the steel pin (15) into the crankshaft slot. Verify the starter gear (62) one-way bearing setup. Manually turn the crankshaft counterclockwise while facing the starter gear. There should be no resistance while turning the starter gear clockwise and no crankshaft rotation.
Start the starter gear (62) by aligning it with the one-way bearing slot so that it just touches the steel pin. Then, insert the starter gear completely using even hand pressure.
Fit the flywheel (75), fastening it with the lock nut (20) and the serrated washer (18).
Put in the front crankshaft bearing (56).
A machinist must machine two countersinks, cut them on the bolts near the camshaft locati0n, and fix them on the timing gear housing (74) (07). It is necessary to swap out two of them for M3x8 countersink bolts.
Install the cross-pin (03) on the camshaft, then the gasket (47) and seal (11) on the timing gear housing. One cap bolt and two countersink bolts secure the timing gear housing.
Ensure the timing gear housing is even with the inside of the gear housing before tightening the two bolts inside. The gasket (47) does not extend down to this bolt position; therefore, proceed cautiously when tightening the outside cap bolts. The mounting lug may bend if the cap bolt is overtightened.
Place the timing gear (53) correctly with the cross-pin on the camshaft. Gently tap the gear to fully engage with the cross pin using a tiny rubber mallet, then insert the e-ring (19) to secure it.
Place the key (16) in the crankshaft slot. Turn the flywheel slowly. This will help the key and timing gear (50) line up.
At the same time, look for the timing marks on both gears (50 and 53). Make sure all three points match up.
Next, engage the timing gear (number 50). Tap the gear using a tiny rubber mallet and tube-shaped tools, then secure it with an e-ring (17).
Screw plug (06) should be inserted into the engine block.
The flywheel is still easily turnable at this point. For every two flywheel revolutions, the three timing markings ought to re-converge.
Apply engine oil to the timing gears. Next, attach the gasket and the timing gear cover. Secure everything with cap bolts. Finally, place the steel pin in position.
Fit the seal retention ring (59), install the front oil seal (09), and secure it with countersink bolts (10).
Using the cross pin (15), install the crank pulley (69). Be very careful not to hit the pulley's surface when tapping the pin in. This can damage the finish.
The flywheel may still spin freely as of right now, albeit there is some resistance. The two oil seals on the crankshaft and the two on the camshaft are primarily responsible for this resistance.
Put the piston in place now (77). Although it is a simple task, each one must be completed individually.
Please don't mix up the piston rings because they are already on the cylinder bore. One by one, push them out so the piston ring gap is about 45 degrees from the crankshaft center line. Next, position the split-bearing alignment mark of the connecting rod so that it faces the pulley end.
To make inserting the piston and ring easier, use the piston ring insertion tool (38). After you tighten the con-rod split bearing bolts, carefully pull the con-rod toward the crankshaft center line with a small screwdriver. It shouldn't move much, which would mean it's not jammed.
Apply a few drops of engine oil to the cylinder wall and con-rod bearing. Because of the tension in the piston rings, the flywheel can be turned, but it will initially feel a little heavy.
Continue with the remaining cylinders. At last, the flywheel rotated with a consistent amount of force.
Turn the engine block over and coat each central and connecting rod bearing with a few drops of engine oil. The oil pan (83) should next be installed with the gasket (43) and fastened with bolts (07). To stop oil leaks, equally tighten the bolts.
Fit the valve tappet (78) into the block of the cylinder. Its working surface must be cleaned, and an oil drop must be on it.
Avoid forcing any tappet into place if it isn't operating smoothly. Utilize the mix-and-match approach. In the end, if steps 1 or 2 don't go smoothly, smooth the brass tube's inner and tappet surfaces with #1,500 emery paper. Then, industrial gasoline is used to clean it.
Place a drop of engine oil on each tappet top once all the tappets are installed. Use a toothpick for support. Press down gently. Turn the flywheel slowly in its normal direction. This means turning it counter-clockwise. The toothpick should be able to glide freely up and down the tappet without experiencing significant resistance.
Ensure no oil is on it and the cylinder block surface is clean. Position the locating steel pins (03) and the cylinder head gasket (40) onto the surface of the cylinder block.
Put the coolant nipple (25) and bore reducer (27), along with the screw plug (05), into the cylinder head (82).
Verify that the cylinder head's (82) valves are operating freely and without binding. After inserting a steel pin into each valve, slide the valve bucket (55) into the recess. Next, examine the push rods (21) and the smoothness again.
After everything checks out, install the cylinder head assembly on the engine block (79) and side cover (02) aligned with the spark plug side. To secure the cylinder head uniformly on the cylinder block, use cylinder head bolts (29) and carefully tighten from the center in a cross pattern.
Fasten the adjustment bolts (22) by tightening them until they become stuck.
Before attaching the valve rocker arms (54) to the adjusting bolts, ensure each set of rocker arms can function with the shaft (61). The collar (23) should then be adjusted, and now is the time to hand-tighten the locking nut (24).
Use #1500 emery paper to smooth out any rough spots on the shaft. This will help the rocker arm work better.
Once all the rocker arms are placed, repeat steps (29) and (30).
Using high-temperature O rings (32) and fastening bolts (30), install the two intake pipes (48) and one exhaust pipe (81).
The valves that connect to the intake manifold are called intake valves. The valves that connect to the exhaust manifold are called exhaust valves.
There is one intake valve and one exhaust valve per cylinder.
While a little challenging, valve adjustment is not difficult. This inline 6-cylinder engine has complimentary cylinders 1-6, 2-5, and 3-4 in order of precedence. The pistons in complementary cylinders have the same action but distinct working strokes.
For instance, the sixth piston likewise rises if the first piston rises. The sixth piston (flywheel end) is on exhaust, and the first piston (pulley end) is on compression. When both valves are entirely closed, which indicates the end of compression, the valves need to be adjusted.
At the point where compression is ending for the first piston, there is no discernible movement of the valve. The rocker arm movement is seen as it transitions from exhaust to suction (intake) on the sixth piston. The firing order for this engine is 1st-4th-2nd-6th-3rd-5th. Next, adjust the valves by the table that follows:
Action: Modifying the cylinder numberFirst 4th 2nd 6th 3rd 5th Observed 1st 4th 2nd 7th
The engine will run better if the valves are adjusted correctly. This adjustment depends on how the other cylinder valves move.
When you turn the flywheel by hand, you can see that the intake valve is open. The exhaust valve on the sixth cylinder is mostly closed. The rocker arm is almost lifting the valve stem.
Next, the two valves on the first cylinder can be changed. Put a 0.2mm aluminum sheet between the rocker arm and the valve bucket, folding it twice with a Coca-Cola can. After that, tighten the lock nut by carefully turning the adjustment collar until it is snug.
The metal sheet can be pushed out with some resistance if it is correctly set and latched. You can lift the rocker arm on the valve side with a small screwdriver. Do this until there is a small gap equal to the thickness of the metal sheet. At that point, everything is just right.
Repeating the process on the remaining cylinders ensures that we observe the proper complementary cylinder valve movement.
Now, engine oil drops can be used to lubricate the valve bucket (55), rocker arm (54), rocker arm shaft (61), and push rod (21).
Turn the flywheel by hand in the usual direction. Keep turning until one cylinder is at the top of the combustion stroke. You can tell this when the intake valve is open and the exhaust valve on the sixth cylinder is just closing.
Apply a small lubricant to the seal (12) and place it inside the timing gear housing recess.
Remove the distributor cap. Position the rotor copper plate at about the eight o'clock position.
Align the distributor shaft driving tang with the camshaft slot. Additionally, the drive belt side should face the silver-colored side of the distributor body. After that, loosen the bolts for a while (13).
Using the bolts (28), install the valve cover (70).
Fix the starter motor (73), fastened with bolts (14).
Use a tiny grindstone to smooth the sharp edge at the crankshaft output end. This is to shield the flywheel bell housing's oil seal from harm.
Attach the flywheel bell housing (68) with bolts (13) after installing the gasket (41) and finding the steel pins (03).
Attach the side cover (72), the gasket (42), the oil nipple (01), and the nipple gasket (02), and fasten it with bolts (36).
Install the throttle synchronized link bar (76) with countersink bolts (35), and then secure the two carburetors (71) with bolts (31).
Install the gasket (85) on the water pump (67) and use cap bolts (34) to secure it temporarily.
Using the fastening bolts (07), install the oil pump mounting bracket (58).
Install the mini-cog belt (45) and oil pump (80) simultaneously. Next, use the cap bolt (08), flange nut (37), and through bolt (36) to adjust and secure it.
Page 27 describes the order of connections for the spark plug wires.
It is possible to supply V8engineforsale oil and coolant pipework.
The factory instruction can be used to refer to starting, running, and maintenance processes.