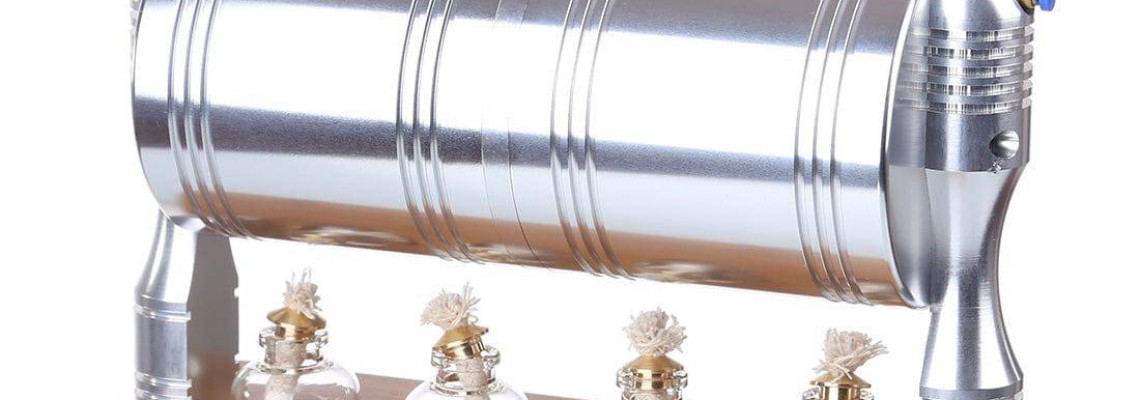
10 Unusual Ways to Produce
Electricity
Heat energy is transformed into mechanical energy and electrical energy when steam power is used to generate Electricity. Usually, a steam turbine connected to a generator is used in this procedure. Here is a broad summary of how steam power is used to create Electricity:
Boiler:
In a boiler, water is heated to produce steam. Burning fossil fuels (oil, coal, or natural gas), employing nuclear processes, or utilizing renewable energy sources like biomass, solar, or geothermal heat can all help achieve this.
Steam Generation:
The steam produced carries thermal energy. The steam's energy content increases with its temperature and pressure.
Steam Turbine:
The steam targets a turbine. By forcing the turbine blades to revolve, steam turbines transform the kinetic energy of the flowing steam into mechanical energy.
Generator:
A generator is attached to the turbine's revolving shaft. The turbine's rotation powers the generator, which transforms mechanical energy into electrical energy.
Power Generation:
The generator produces electrical power, usually in the form of alternating current (AC). Transformers can then increase the voltage of this Electricity for effective long-distance transmission.
Condenser:
After passing through the turbine, the steam is converted back into water in a condenser. To finish the cycle, the released latent heat is often transported to a cooling medium, such as air or water.
Cooling System:
The heat from the condensing steam is absorbed by the cooling medium and transformed back into liquid water. After cooling, the water is put back into the boiler to be heated again and utilized again to create steam.
Control Systems:
A variety of sensors, control systems, and monitoring tools maximize the power plant's safety and efficiency. These systems control temperature, steam pressure, and other factors to guarantee efficient functioning.
Known as a Rankine cycle, this technique is widely used in power plants worldwide to generate Electricity. Depending on the type of power plant, the heat source may be derived from renewable energy sources or fossil fuels. The design of the turbine and generator, the temperature and pressure levels, and the cooling system selection all affect the system's overall efficiency.
10 Unusual Ways to Produce Electricity: Steam Power
Boiler:
An essential part of a system that generates steam power is the boiler. Its main purpose is to use heat from combustion or another heat source to turn water into steam. After leaving the boiler, the steam is sent to a steam turbine, where it expands and generates energy by performing mechanical work. Here are further boiler-related details:
Function: The boiler is an essential part that heats water to create high-pressure steam. The source of heat may differ:
Fossil fuels: Burning coal, oil, or natural gas.
Nuclear: Heat from nuclear processes creates
steam.
Renewable Energy: Geothermal, solar, and biomass energy sources are also viable.
Types of Boilers:
Fire-tube Boilers:
Construction: Tubes carrying hot combustion gasses are encircled by water.
Benefits: Small to medium-sized applications can benefit from its straightforward design and relatively compact size.
Applications: Frequently utilized in smaller power plants and industrial activities.
Water-Tube Boilers:
Construction: Combustion fumes heat the tubes in which water circulates.
Benefits: Increased effectiveness, increased capacity, and resistance to increased pressure.
Applications: Frequently seen in industrial settings and big power plants.
Once-Through Boilers:
Operation: There is no recirculation; water goes through the boiler once.
Benefits: Effective functioning at varied loads and quick startup.
Applications: Frequently found in various contemporary power plants, especially when combined with steam conditions that are supercritical and ultra-supercritical.
Boiler Components:
Furnace:
Function: Heat is released during the combustion of fuel (coal, natural gas, oil, and biomass) in the furnace.
Combustion Chamber: The space where fuel burns and produces combustion gasses.
Water Walls:
Location: These are the water-filled tubes that round the furnace in water-tube boilers.
Goal: Produce steam by absorbing furnace heat.
Function: Gathers and extracts water and steam. It also acts as a reservoir for the steam that is produced from water.
Circulation: Assists in keeping the boiler's water flowing properly.
Superheater:
Location: Usually positioned following the steam drum.
Function: Increases the energy content and efficiency of steam by raising its temperature to a higher level (superheated steam).
Economizer:
Location: Usually found in the path of flue gas.
Function: Increases overall efficiency by utilizing the remaining heat from the flue gases to preheat the feedwater.
Boiler Burners:
Function: Burners are where fuel is burned.
Types: Depending on the fuel type, they can be solid fuel burners, gas burners, or oil burners.
Boiler Operation:
Fuel Input:
Combustion Process: The furnace burns flammable materials, such as fossil fuels.
Control Systems: To ensure ideal combustion conditions and regulate the fuel and air supply.
Water Circulation:
Natural Circulation: Uses variations in density to move water.
Forced Circulation: Pumps are utilized to guarantee adequate water circulation in larger boilers.
Steam Generation:
Heat Transfer: Steam is created when heat from the combustion process is transferred to water.
Control of Pressure and Temperature: Systems manage the temperature and pressure of steam.
Boiler Safety:
Pressure Relief Devices:
Safety Valves: To avoid overpressurization, release excess pressure.
Safety Interlocks: Automated emergency shutdown mechanisms.
Water Level Control:
Preventing Dry Firing: Maintains a sufficient water level to shield the boiler from harm.
Combustion Control:
Fuel-Air Ratio: Maintained for efficient and safe combustion.
Emission Control: Keeping an eye on emissions and managing them to ensure environmental compliance.
Comprehending the many kinds of boilers, their parts, and how they work is essential to guarantee the safe and effective production of steam for Electricity. For a boiler system to operate dependably, regular maintenance, observation, and adherence to safety procedures are necessary.
Steam Generation:
In power plants, steam generation is a basic process that turns water into steam, which powers turbines that are connected to generators to produce Electricity. The following are the main elements of steam generation:
Boiler:
Function: The main element in charge of producing steam is the boiler.
Process: The water inside the boiler is heated using various heat sources, including nuclear processes, the burning of fossil fuels, and renewable energy sources like biomass, solar, or geothermal heat.
Collection and Separation: The steam produced in the boiler is gathered and separated from the water in the steam drum.
Water Circulation:
Natural Circulation: The boiler's natural circulation is based on the density difference between steam and hot water.
Forced Circulation: In large installations, pumps are employed to move water through the boiler.
Superheating:
Superheater: Superheated steam is created when steam passes through a superheater, which raises the steam's temperature above the boiling point.
Benefits: The specific enthalpy and energy content of superheated steam are increased.
Quality of Steam:
Dry Steam: Steam that contains very little moisture.
Wet Steam: Steam that has water droplets entrained in it.
Steam Parameters:
Pressure: Because it influences the temperature and energy content, the steam's pressure is an important factor.
Temperature: Higher temperatures lead to higher efficiency and energy content.
Heat Transfer:
Convection: Heat transfer via fluid movement (steam or water) inside the boiler.
Radiation: Heat transfer by electromagnetic waves.
Conduction: Direct transfer of heat between materials.
Steam Quality Control:
Separators: Before steam enters the turbine, they are used to eliminate any last traces of water.
Control Systems: Keep an eye on and adjust steam settings to ensure safe and effective operation.
Heat Recovery:
Economizer: Preps the feedwater before it enters the boiler by recovering heat from flue gasses.
Recuperator: Recovering heat from flue gases is another kind of heat exchanger.
Cogeneration:
Combined Heat and Power (CHP): Some systems are made for cogeneration, in which steam generates heat for homes or businesses in addition to Electricity.
Expansion: Steam is sent from the boiler to the steam turbine, where it rotates the turbine blades to produce mechanical work.
Efficiency Considerations:
Thermal Efficiency: A key component of total power plant efficiency is the effectiveness of the steam production process.
Irreversibilities: Efficiency is impacted by systemic losses brought on by irreversibilities.
Environmental Impact:
Emission Control: Technologies to reduce emissions and their negative effects on the environment may be included in fossil fuel-based systems.
Startup and Shutdown Procedures:
Warm-Up Time: In order to achieve operating conditions, boilers must go through a warm-up time.
Cool-Down Period: To prevent heat stress on components, proper measures are followed during shutdown.
Optimizing power plant efficiency, guaranteeing dependable operation, and reducing environmental impact all depend on an understanding of the subtleties of steam generation. Technological developments keep making power plants' steam generation procedures more efficient.
Procedure: High-pressure steam is created by heating water that is pumped into the boiler.
Parameters: The system's efficiency is mostly dependent on the temperature and steam pressure.
A steam turbine is a mechanical device that uses high-pressure steam energy to generate mechanical work that is then transformed into electrical power. In many facilities, this process is essential to the production of Electricity.
The turbine is filled with high-pressure steam, which passes across rotor-mounted blades. These blades effectively harness the steam's energy, turning the rotor. The steam turbine generates mechanical work through the rotor's rotational motion. This rotating action turns a generator attached to the turbine shaft. Using electromagnetic induction, the generator transforms mechanical energy into electrical energy.
After transferring its energy to the blades, the steam leaves the turbine at a reduced temperature and pressure. The steam may occasionally condense back into water so that it can be used again in the boiler.
Different designs are available for steam turbines. In impulse turbines, steam expands in nozzles to produce high-velocity jets that strike turbine blades. In contrast, steam in reaction turbines expands across turbine blades and in nozzles, generating a mix of pressure and kinetic energy.
From major utility-scale power plants to small-scale industrial facilities, these turbines are used in a variety of power plants. Their effectiveness, dependability, and flexibility in handling various steam conditions make them highly prized.
Continuing developments in turbine technology and design aim to improve overall performance and efficiency, which helps power generation systems improve over time. Steam turbines' adaptability makes them essential parts of the world's energy system.
Function: The turbine rotates as a result of the steam being directed onto the turbine blades.
Types: Steam turbines come in a variety of forms, such as impulse and reaction turbines.
What is a Steam Turbine?
For more than a Century, steam turbines have been a vital component of industrial power generation because they offer a dependable and effective way to transform thermal energy into mechanical energy. Steam turbines are essential to many industrial operations and the production of Electricity, making them a key part of the world's energy system. Power plants and the petrochemical industry are only two of the industries that have found them invaluable due to their great operating efficiency and versatility.
This article aims to provide a thorough analysis of steam turbines, emphasizing their construction, functionality and uses in addition to the most recent technological developments influencing their evolution. This comprehensive handbook, intended for specialists in the area, attempts to improve comprehension and enable well-informed decision-making in the implementation and administration of steam turbine technology.
This article will explore the development of steam turbines over time, looking at significant turning points that have shaped their advancement. It will go over the basic ideas that underlie their functioning, such as the mechanical elements and thermodynamic processes that propel them. Additionally, the page will classify several steam turbine models, emphasizing their unique benefits and uses.
This book will also discuss the advantages and disadvantages of steam turbines, offering a fair assessment of their effects on the environment and the economy. We'll examine current developments and emerging trends in steam turbine technology to guide future research and development.
The essay will cover the operational difficulties and maintenance needs related to steam turbines in addition to their technical features, emphasizing how crucial appropriate maintenance is to guarantee their longevity and effectiveness. Readers will learn important lessons about best practices and methods for overcoming typical challenges by looking into case studies of turbine failures and recoveries.
The overall goal of this essay is to be a useful tool for experts who want to learn more about steam turbines and how they are used in contemporary industrial processes and power generation.
History of Steam Turbines
The late 19th Century, a time of great invention and economic expansion, is when steam turbines first appeared on the scene. Since the efficiency and capacity of conventional steam engines were constrained, the desire for more effective power-generating techniques led to the development of steam turbines. The historical turning points and influential people that have influenced the development of steam turbines over time will be examined in this section.
Early Development and Pioneers
Early inventions like the Aeolipile, created by Hero of Alexandria in the first century AD, showcased the potential of steam power. Harnessing steam to perform mechanical tasks has ancient roots. However, steam technology didn't start to grow quickly until the 19th Century, when the steam turbine was created.
The modern steam turbine was created in 1884 and is credited to Sir Charles Parsons. In contrast to the reciprocating steam engines of the era, Parsons' design used a number of revolving blades to transform steam energy into rotational motion. His creation, which offered increased power output and efficiency, transformed power generation. The Turbinia, a steam-powered ship that displayed the possibilities of this new technology, hosted the first demonstration of Parsons' steam turbine in 1897.
In 1883, Swedish inventor Gustaf de Laval created an impulse steam turbine that struck blades linked to a rotor with a high-velocity steam jet. Applications needing high rotational speeds, like small-scale power generation and centrifugal pumps, were especially well-suited for De Laval's design.
Evolution Over the 20th Century
Steam turbine technology advanced quickly in the early 20th Century due to growing industrial activity and the need for power. Steam turbines' exceptional efficiency and capacity to run continuously under heavy loads made them the go-to option for power generation very rapidly.
Sir Charles Parsons' invention of the reaction turbine was one of the major advancements of the time. Reaction turbines use the pressure differential across the blades to generate rotational motion, as opposed to impulse turbines, which depend on steam jets to provide the blades with momentum. Large power plants embraced this design because it made energy conversion more efficient.
The development of sectors like steel, chemicals, and transportation, as well as the extension of the electrical grid, further increased the need for steam turbines. The creation of high-strength alloys and other developments in materials science allowed turbines to function at higher pressures and temperatures, improving their dependability and efficiency.
Key Technological Milestones
Several significant technological turning points have characterized the development of steam turbines over the years:
Supercritical Steam Conditions: The advent of supercritical steam conditions in the middle of the 20th Century made a major advancement in turbine efficiency possible. Supercritical turbines ran at pressures and temperatures above the critical point of water, attaining higher thermal efficiency and lower fuel consumption.
Combined Cycle Power Plants: Adding steam turbines to combined cycle power plants, which generate steam from gas turbine waste heat, increased plant efficiency even more. This method reduced the impact on the environment while optimizing the amount of energy extracted from fuel.
Nuclear Power Generation: Steam turbine technology saw new prospects with the introduction of nuclear power in the middle of the 20th Century. Since nuclear reactors generate a lot of steam, steam turbines are a perfect option for nuclear power facilities looking to generate energy.
Digital Control Systems: In the late 20th Century, digital control systems were introduced, which improved the dependability and operational efficiency of steam turbines. Thanks to advanced monitoring and control systems, turbine parameters could be precisely adjusted, enhancing performance and decreasing downtime.
Basic Principles of Operation
Based on the laws of thermodynamics, steam turbines use a sequence of meticulously planned procedures to transform the thermal energy of steam into mechanical energy. This section will cover the basic ideas behind steam turbine functioning, along with the thermodynamic cycles and the kinds of turbines that are frequently employed in different applications.
Thermodynamics of Steam Turbines
The transformation of thermal energy into mechanical work is the fundamental process of steam turbine functioning. The laws of thermodynamics, which explain the connections between heat, work, and energy, control this process. The Rankine cycle, a thermodynamic cycle that includes the following crucial events, is the main mechanism by which steam turbines function:
Boiler (Heat Addition): High-pressure steam is created in the boiler by heating water. The turbine's main energy source is steam, which is usually superheated to boost efficiency.
High-pressure steam is fed into the turbine, where it expands and transfers energy to the turbine blades. This process is known as the turbine (expansion and work extraction). When the steam expands and experiences a drop in temperature and pressure, the turbine rotor rotates and generates mechanical work.
Condenser (Heat Rejection): After passing through the turbine, the low-pressure steam is converted back into water in the condenser. This eliminates extra heat from the system, and the water may be recycled back into the cycle.
Pump (Pressurization): To finish the cycle, the condensed water is pumped back to high pressure and sent back to the boiler.
Temperature, steam pressure, and the efficiency of the condensation process are some of the variables that affect a steam turbine's efficiency. By fine-tuning these factors, engineers can reduce losses and increase energy conversion efficiency.
Types of Steam Turbines
Impulse turbines and reaction turbines are the two basic categories of steam turbines. Each type is appropriate for particular purposes and functions according to different principles.
Impulse Turbine: An impulse turbine rotates its blades by directing high-velocity steam jets onto them. Energy is exchanged between the blades through the change in steam velocity, while the steam pressure stays constant. High rotational speed applications, such as maritime propulsion and small-scale power generation, frequently employ impulse turbines.
Reaction Turbines: Reaction turbines generate rotational motion by using the pressure drop across the blades. The pressure and velocity changes that the steam undergoes as it passes between the blades result in a more constant energy transfer. Because of their increased efficiency and capacity to handle high steam volumes, reaction turbines are frequently utilized in large power plants and industrial settings.
The Rankine Cycle
The thermodynamic cycle that drives steam turbine operation is called the Rankine cycle. Its effectiveness is a major factor in determining the overall performance of the turbine and is comprised of a sequence of processes that transform thermal energy into mechanical work. Four primary steps define the Rankine cycle:
Isentropic Expansion: High-pressure steam converts its energy into mechanical work in the turbine through isentropic expansion, which is adiabatic—that is, no heat is transmitted to or from the system.
Isobaric Heat Rejection: The low-pressure steam experiences isobaric heat rejection as it enters the condenser following expansion. Heat is released into the environment as the steam cools and condenses into liquid water.
Isentropic Compression: In the feed pump, the condensed water is pumped back to high pressure, where it undergoes isentropic compression. This technique is adiabatic and raises the water's pressure without generating additional heat.
Isobaric Heat Addition: Lastly, the high-pressure water is put back into the boiler to go through this process. The cycle is completed by heating the water and turning it into high-pressure steam.
The temperature and pressure of the steam, the efficiency of the condenser, and the level of superheating are some of the variables that affect the Rankine cycle's efficiency. Engineers tune these parameters to increase steam turbine efficiency and reduce fuel consumption.
Design and Components
Steam turbine design is a complicated technical undertaking that requires the integration of several parts and materials to obtain the best possible performance and dependability. This section examines the main design features and components of steam turbines, along with the difficulties and factors that must be taken into account during construction.
Major Components
Each of the essential parts that make up a steam turbine is essential to the process of converting thermal energy into mechanical work. A steam turbine's main parts are as follows:
Rotor: The rotor is the central shaft that transfers the mechanical energy produced by the steam and sustains the turbine blades. To endure the strains and heat experienced during operation, it is usually constructed from high-strength materials, like forged steel.
Blades: The airfoil-shaped parts that interact with the steam flow to create rotating motion are called blades, sometimes referred to as buckets or vanes. Blades are meticulously constructed to maximize energy extraction and minimize losses from friction and turbulence.
Casing: The turbine is enclosed by the casing, also known as the housing, which guides the steam flow through the blades. In addition to providing structural support, it aids in preserving the turbine's ideal temperature and pressure levels.
Nozzles: In impulse turbines, nozzles direct high-velocity steam jets onto the turbine blades. To achieve the required steam velocity and flow parameters, nozzle design is essential.
Bearings: The rotor is supported by bearings, which provide smooth rotation with little friction. They are usually lubricated to minimize wear and heat generation and are made to withstand both axial and radial loads.
Governor: By modifying the steam flow, the governor is a control device that manages the turbine's speed and output. It guarantees that the turbine responds to variations in load demand and system conditions while operating within safe and effective bounds.
Materials Used in Construction
The selection of materials for steam turbine construction is based on their resistance to high pressures, temperatures, and mechanical stresses. Important material factors consist of the following:
High-Temperature Alloys: Superalloys based on nickel or cobalt are frequently used to make turbine parts that are subjected to high temperatures, such as rotors and blades. At high temperatures, these materials show outstanding strength and resistance to corrosion, oxidation, and creep.
Stainless Steel: Because of its durability and resistance to corrosion, stainless steel is frequently used for turbine casings and other structural elements.
Titanium: Because of its high strength-to-weight ratio and resilience to corrosion and fatigue, titanium alloys are occasionally utilized in turbine blades.
Ceramics and Composites: Advanced ceramics and composite materials are being investigated for application in steam turbines to increase efficiency and decrease weight. These materials have the potential to be advantageous in terms of wear resistance and thermal insulation.
Design Considerations and Challenges
For steam turbines to operate as efficiently and reliably as possible, a number of intricate factors and difficulties must be taken into account during design. Important design considerations are:
Thermal Efficiency: One of the main objectives of turbine design is to maximize thermal efficiency. This entails maximizing energy extraction from the steam, minimizing friction and turbulence losses, and optimizing the thermodynamic cycle.
Mechanical Stress and Fatigue: Turbine components are exposed to severe mechanical strains and cyclic loading during operation. To guarantee the turbine's robustness and dependability, engineers must closely examine stress distributions and fatigue life.
Noise and Vibration: Steam turbine lifespan and performance can be impacted by noise and vibration. To lessen these impacts, design techniques like damping, balancing, and noise reduction techniques are used.
Cooling and Heat Management: Efficient cooling and heat management are crucial to avoid overheating and guarantee the turbine's safe operation. This includes choosing materials with the right thermal qualities and designing cooling methods, including air or steam cooling.
Environmental Impact: Reducing steam turbines' negative effects on the environment is crucial. This entails cutting emissions, increasing productivity, and creating sustainable and recyclable designs.
Types of Steam Turbines
Different types of steam turbines are distinguished by their size, intended use, and design features. This part examines these various kinds of steam turbines, emphasizing their unique characteristics and uses.
Classification by Size and Application
Based on their size and intended use, steam turbines can be roughly divided into three types:
Industrial Steam Turbines: Industrial steam turbines are typically employed for mechanical drive and power generation in the manufacturing and process industries. They come in a variety of sizes, from tiny devices that only produce a few kilowatts to massive turbines that produce many megawatts. Industrial turbines can function effectively under a range of load circumstances because they are frequently made to be flexible.
Utility Steam Turbines: These massive turbines are utilized in power plants to provide Electricity for the grid. With capacities ranging from hundreds of megawatts to more than a gigawatt, they are built for high efficiency and dependability. Utility turbines are frequently found in combined-cycle power plants, where they complement gas turbines to optimize energy production.
Specialized Steam Turbines: These turbines are made for particular uses, such as nuclear, geothermal, and marine propulsion. They are designed to meet the specific needs and circumstances of their respective sectors, such as managing corrosive steam in geothermal facilities or functioning in a ship's limited area.
Industrial Steam Turbines
Industrial steam turbines are adaptable devices with a variety of uses, such as:
Combined Heat and Power (CHP) and Cogeneration Systems: In CHP and cogeneration systems, industrial turbines are frequently employed to produce Electricity and process heat for industrial operations. This method decreases waste and increases energy efficiency.
Mechanical Drives: In sectors including pulp and paper, petrochemicals, and oil and gas, steam turbines are employed as mechanical drives for machinery like fans, pumps, and compressors.
District Heating: To heat homes and businesses, district heating systems use steam produced by industrial turbines to provide energy. This combined strategy lowers emissions while improving energy use.
Utility Steam Turbines
In many nations, utility steam turbines are the main source of Electricity, supplying the grid with dependable and effective power. Utility turbines' salient characteristics include:
High Efficiency: With sophisticated blade designs and optimized thermodynamic cycles, utility turbines are built to operate as efficiently as possible. This enables them to minimize fuel usage and maximize the energy extracted from the steam.
Load Flexibility: Utility turbines can adapt to changes in power demand by operating under a variety of load circumstances. The grid's stability and dependability depend on this flexibility.
Combined Cycle Operation: A large number of utility turbines are used in combined cycle power plants, where they cooperate with gas turbines to reduce emissions and increase energy output. This arrangement increases plant efficiency by using the gas turbine's waste heat to generate steam for the steam turbine.
Specialized Steam Turbines
Specialized steam turbines are made to satisfy particular applications' and industries' particular needs. Some examples are as follows:
Geothermal Steam Turbines: These turbines run on steam drawn from geothermal reservoirs, which frequently contain corrosive contaminants. Materials and coatings resistant to corrosion and scaling are used in the construction of these turbines.
Nuclear steam turbines: In atomic power plants, atomic turbines generate Electricity from the steam generated by nuclear reactors. They must adhere to strict safety and regulatory standards and are made to withstand the high temperatures and pressures associated with atomic steam.
Marine Steam Turbines: Marine turbines propel ships and submarines. They are built to be dependable and small and feature features like gear reduction systems to maximize performance in aquatic settings.
Applications of Steam Turbines
Steam turbines' efficiency and versatility make them useful in a wide range of industries. This section will examine steam turbines' various uses, emphasizing their use in industrial operations, power generation, and other fields.
Power Generation in Different Sectors
An essential component of power generation, steam turbines produce dependable and effective Electricity for use in homes, businesses, and industries. Important uses for Electricity generating include:
Fossil Fuel Power Plants: Heat energy from burning coal, oil, or natural gas is converted into electrical power in fossil fuel power plants using steam turbines. These plants, which have sophisticated turbines built for great efficiency and low emissions, are a significant source of Electricity in many nations.
Nuclear Power Plants: Steam turbines in nuclear power plants produce energy from heat produced by nuclear fission. These reactors' turbines must meet strict safety and regulatory requirements and are built to withstand the high temperatures and pressures associated with atomic steam.
Renewable Energy Sources: Geothermal and biomass power plants are two examples of renewable energy applications that use steam turbines. Steam drawn from subterranean reservoirs powers turbines in geothermal facilities, producing energy. Turbines in biomass plants generate energy using steam created by burning organic materials.
Use in Combined Heat and Power (CHP) Systems
Cogeneration, another name for Combined Heat and Power (CHP) systems, is an effective way to produce both useful heat and Electricity at the same time. In CHP systems, steam turbines are essential because they deliver the mechanical energy required to generate Electricity and steam for industrial and heating activities. CHP systems are used in the following applications:
Industrial Facilities: CHP systems are frequently found in industrial facilities, where they generate steam for manufacturing processes and supply energy. This comprehensive strategy lowers waste and improves energy efficiency, which saves money and benefits the environment.
District Heating: Steam turbines produce energy and supply steam for heating homes and businesses in district heating systems. By lowering emissions and improving energy use, this strategy promotes sustainable urban growth.
Hospitals and Universities use CHP systems to offer dependable heating and Electricity. Energy security is improved, and operating expenses are decreased when a single fuel source can be used to produce both power and heat.
Role in Industrial Processes
Steam turbines are essential to many industrial processes because they supply heat and mechanical power for production and processing. Important uses in industrial operations consist of the following:
Petrochemical Industry: Compressors, pumps, and other machinery used in the manufacturing and refinement of chemicals and fuels are powered by steam turbines in the petrochemical industry. Steam turbines are ideal for demanding industrial applications due to their great efficiency and dependability.
Pulp and Paper Business: The pulp and paper business uses steam turbines to produce energy and supply steam for the pulping and drying procedures. Utilizing steam turbines in these processes improves energy efficiency and lessens the impact on the environment.
Food and Beverage sector: The food and beverage sector uses steam turbines to supply Electricity and steam for cooking, sterilizing, and other procedures. Integrating steam turbines into cogeneration systems makes cost savings and effective energy use possible.
Advantages and Disadvantages
Although steam turbines offer many benefits in terms of effectiveness, dependability, and adaptability, they also have several drawbacks and restrictions. This section will present a fair assessment of the advantages and disadvantages of steam turbines by contrasting them with alternative power production methods.
Advantages of Steam Turbines
High Efficiency: Steam turbines' ability to efficiently transform thermal energy into mechanical work is well-known. Thanks to advanced designs and materials, turbines in contemporary power plants can now achieve thermal efficiencies of above 40%.
Reliability and Durability: Steam turbines can run continuously for extended periods under heavy loads because they are incredibly dependable and robust. They require little maintenance and have a long service life because of their sturdy structure and materials.
Low Emissions: When combined with cutting-edge combustion and emission control technologies, steam turbines can produce low emissions. For instance, steam turbines are used in combined-cycle power plants to lower greenhouse gas emissions and increase total plant efficiency.
Scalability: Because steam turbines come in a variety of sizes and capacities, they can be used in both small- and large-scale settings. This scalability makes flexible implementation across a range of settings and businesses possible.
Disadvantages of Steam Turbines
Cost and Complexity: Steam turbine design and construction are expensive and need sophisticated engineering. The requirement for sophisticated control systems, precise manufacture, and specific materials influences the total cost of installing and maintaining a turbine.
Startup Time: Compared to other power production technologies, including gas turbines, steam turbines require a comparatively long startup time. The boiler must be heated to operating temperatures, which may delay reacting to variations in the demand for power.
Water Consumption: Because steam turbines generate and cool steam using water, their operation is reliant on water availability. This may cause difficulties in areas with scarce water supplies or during dry spells.
Environmental Impact: Although steam turbines can produce low emissions, the kind of fuel they use and the system's overall efficiency impact their environmental friendliness. Steam turbines that run on fossil fuels cause air pollution and greenhouse gas emissions.
Maintenance Requirements: To guarantee optimum performance and avoid problems like corrosion, fouling, and wear, steam turbines need routine maintenance. Because of their complexity, turbine systems require specialized equipment and trained staff for upkeep and repair.
Comparison with Other Power Generation Technologies
Other power production methods, including gas turbines, internal combustion engines, and renewable energy systems, are frequently contrasted with steam turbines. Important analogies include:
Gas Turbines: Compared to steam turbines, gas turbines have quicker startup times and more flexibility, which makes them ideal for peaking power plants and fast reactions to variations in the demand for Electricity. On the other hand, steam turbines are better suited for base-load power generation and usually attain higher thermal efficiency.
Internal Combustion Engines: Although internal combustion engines are small and ideal for producing Electricity on a small scale, they are less effective and emit more pollutants than steam turbines. For large-scale applications where dependability and efficiency are crucial, steam turbines are the chosen option.
Renewable Energy Systems: The benefits of renewable energy systems, including solar and wind, include sustainability and zero emissions. However, because of their capacity to deliver dependable base-load power and facilitate the integration of intermittent renewable sources, steam turbines continue to be an essential part of the energy mix.
Recent Technological Advancements
The need for increased efficiency, dependability, and environmental performance has spurred major developments in steam turbine technology in recent years. This section will examine current developments in steam turbine design, materials, and control systems to illustrate the trends influencing steam turbine technology in the future.
Innovations in Design and Materials
The goal of developments in steam turbine materials and design has been to improve performance and efficiency while lessening their negative effects on the environment. Among the major innovations are:
Advanced Blade Designs: The advanced blade designs found in modern steam turbines are intended for lower losses and aerodynamic performance. To improve energy extraction and decrease turbulence, blade designs are modeled and refined using computer-aided design (CAD) and computational fluid dynamics (CFD) technologies.
High-Temperature Materials: By enabling turbines to function at greater temperatures and pressures, high-temperature materials—such as ceramics and nickel-based superalloys—have improved thermal efficiency and decreased fuel consumption. Their exceptional resistance to corrosion, oxidation, and creep ensures long-term durability.
3D Printing and Additive Manufacturing: Using additive manufacturing techniques like 3D printing, complex turbine components are being produced with high precision and shorter lead times. This technique allows for lightweight and complex designs that improve performance and lower manufacturing costs.
Cooling Technologies: To control heat and increase efficiency, sophisticated cooling technologies have been developed, such as air-cooled and steam-cooled systems. By minimizing the chance of overheating and optimizing temperature dispersion, these cooling systems improve turbine dependability.
Digitalization and Control Systems
Steam turbine maintenance and operation are changing due to digitalization and sophisticated control systems, which present new chances for efficiency and optimization. Important advancements in this field include:
Digital Twins: Digital twin technology enables real-time modeling, analysis, and monitoring by building a virtual model of a real turbine. Predictive maintenance, performance optimization, and troubleshooting are made possible by digital twins, which lower operating expenses and downtime.
Advanced Diagnostics and Monitoring: State-of-the-art sensors and monitoring systems installed in contemporary steam turbines offer real-time information on critical parameters, including vibration, temperature, and pressure. Proactive maintenance and decision-making are made easier by these technologies, which also allow for early problem detection.
Automated Control Systems: Computerized control systems, powered by artificial intelligence and machine learning algorithms, optimize turbine operation by modifying parameters in response to shifting conditions. These systems increase overall performance, lower emissions, and boost efficiency.
Remote Monitoring and Control: Remote monitoring and control capabilities enable operators to monitor turbine performance from a central location, improving operational efficiency and allowing prompt problem-solving. This technique is especially useful for overseeing sizable turbine fleets spread over several places.
Future Trends in Steam Turbine Technology
Ongoing research and development initiatives to increase efficiency, sustainability, and integration with new energy systems will influence steam turbine technology in the future. Important trends consist of:
Integration with Renewable Energy: To increase efficiency and supply dependable base-load electricity, steam turbines are increasingly being integrated with renewable energy systems, such as solar thermal and geothermal. Hybrid systems that integrate steam turbines with renewable energy sources are anticipated to influence the energy landscape significantly in the future.
Decarbonization and Emissions Reduction: Initiatives to lessen carbon emissions and their negative environmental effects are propelling advances in steam turbine technology. The main goals of lowering steam turbines' carbon footprint are enhanced efficiency, innovative combustion technologies, and carbon capture and storage (CCS) systems.
Energy Storage and Grid Integration: To improve grid stability and facilitate the integration of intermittent renewable sources, the combination of steam turbines with energy storage devices, such as batteries and thermal storage, is being investigated. By facilitating flexible and dependable power generation, these systems help strengthen the energy grid's resilience.
Micro and Small-Scale Turbines: For off-grid and decentralized power generation, there is growing interest in the development of micro and small-scale steam turbines. These turbines can improve energy security and provide localized energy solutions, especially in isolated and underdeveloped locations.
Maintenance and Operational Challenges
To guarantee optimum performance, dependability, and lifetime, a number of issues related to steam turbine operation and maintenance must be resolved. This part examines the common maintenance and operational problems with steam turbines and recommends practices and solutions.
Common Issues and Solutions
A variety of operational issues can affect the performance and efficiency of steam turbines, which are intricate devices. Typical problems include:
Erosion and corrosion are major problems in steam turbines, especially for parts subjected to harsh conditions and high temperatures. These problems can result in shorter component lifespans, higher maintenance expenses, and decreased efficiency. Some solutions include using materials resistant to corrosion, applying protective coatings, and maximizing steam chemistry to reduce corrosive agents.
Fouling and Deposits can build up on turbine parts, decreasing heat transfer effectiveness and affecting operation. Sophisticated filtration and water treatment systems, as well as routine cleaning and maintenance, can reduce fouling and deposits.
Vibration and Noise: Engineers employ methods like balancing, damping, and vibration analysis to pinpoint and resolve the sources of vibration and noise, which can impair steam turbine performance and lifespan and possibly result in mechanical failures and operational disruptions.
Thermal Stress and Fatigue: Steam turbines are prone to thermal stress and fatigue due to cyclic loading and temperature variations. Cracking, distortion, and other structural problems may result from these circumstances. To reduce thermal stress and fatigue, engineers employ thermal management techniques, innovative materials, and design optimization.
Seal and Gasket Failures: Proper selection, installation, and maintenance of seals and gaskets are necessary to ensure reliable operation. Seals and gaskets are essential components that prevent leaks and maintain pressure differentials within the turbine; failures can result in decreased efficiency and increased maintenance requirements.
Importance of Regular Maintenance
For steam turbines to operate dependably and effectively, routine maintenance is essential. Important maintenance procedures consist of the following:
Scheduled checks: Routine checks are crucial to spot possible problems and ensure turbine parts are in good shape. Visual inspections, non-destructive testing, and performance reviews are a few possible inspection methods.
Predictive Maintenance: Predictive maintenance methods like vibration analysis and thermal imaging track turbine performance and spot possible problems before they become serious. This proactive strategy lowers maintenance expenses and downtime.
Lubrication Management: Proper lubrication is crucial to reducing wear and friction in turbine components. Lubrication systems that receive routine monitoring and maintenance operate at their best and have longer component lifespans.
Cleaning and Servicing: Turbine components must be cleaned and serviced to remove deposits, fouling, and other impurities that can affect performance. Frequent cleaning lowers the chance of mechanical problems and increases heat transfer efficiency.
Calibration and Adjustment: To ensure precise and dependable functioning, control systems, sensors, and actuators must be calibrated and adjusted. Turbines function within safe and effective parameters when they are regularly calibrated.
Case Studies of Failure and Recovery
Case studies of steam turbine recoveries and failures offer important insights into operating issues and best practices. Among the examples are:
Turbine Blade Failure: A turbine blade failure caused by fatigue cracking abruptly caused a power station to lose power. According to an investigation, the failure was caused in part by poor maintenance and inspection. To avoid future problems, the factory implemented a thorough maintenance program that included routine inspections and predictive maintenance methods.
Corrosion-Induced closure: The steam path of a turbine experienced corrosion, resulting in a protracted closure at a chemical processing complex. The plant reduced corrosive agents by implementing a steam chemistry optimization program and enhancing corrosion resistance with modern materials and coatings.
Vibration-Related Performance Issues: Excessive vibration in a paper mill's steam turbines led to decreased efficiency and higher maintenance expenses. To solve the problem, engineers carried out a thorough vibration analysis and implemented balancing and dampening measures, which enhanced performance and dependability.
Conclusion
Because they provide dependable and effective power generation for a range of sectors and applications, steam turbines continue to be an essential part of the worldwide energy landscape. This page thoroughly covers steam turbine history, design, operation, and applications, as well as current technological developments and maintenance issues.
Summary of Key Points
Historical Development: Since their creation in the late 19th Century, steam turbines have seen substantial development, with gains in performance and efficiency being driven by developments in design, materials, and technology.
Principles of Operation: Using the Rankine cycle, steam turbines transform thermal energy from steam into mechanical work in accordance with the laws of thermodynamics. Temperature, steam pressure, and the efficiency of the condensation process are some of the variables that affect the performance and efficiency of steam turbines.
Design and Components: Rotors, blades, casings, and nozzles are just a few of the components that must be integrated into the design of steam turbines. Developments in materials and manufacturing processes have improved turbine performance and dependability.
Applications: Power generation, industrial operations, and combined heat and power (CHP) systems are just a few of the many uses for steam turbines. Many industries choose them because of their efficiency and adaptability.
Benefits and Drawbacks: While steam turbines have many benefits, including high efficiency, dependability, and scalability, they also have certain drawbacks, such as complexity, expense, and environmental effects.
Technological Developments: New developments in steam turbine technology, such as design, material, and digitalization breakthroughs, are influencing the industry's future and improving sustainability and efficiency.
Operational and Maintenance Difficulties: Steam turbines pose a number of operational and maintenance difficulties, such as thermal stress, vibration, corrosion, and fouling. Best practices and routine maintenance are crucial to guarantee optimum performance and dependability.
Future Outlook for Steam Turbines
Ongoing research and development initiatives to increase efficiency, sustainability, and integration with new energy systems will influence steam turbines' future. Steam turbines are anticipated to be crucial in facilitating the shift to a more robust and sustainable energy future as the energy environment changes further. Important areas of attention consist of:
Decarbonization: Efforts to lower carbon emissions and their effects on the environment will fuel innovations in steam turbine technology, including carbon capture and storage (CCS) systems and better combustion technologies.
Combining steam turbines with renewable energy sources, such as geothermal and solar thermal, will increase efficiency and offer dependable base-load power, helping create a more sustainable energy mix.
Automation and Digitalization: Improvements in automation and digitalization will allow steam turbines to operate more dependably and efficiently, saving maintenance costs and improving performance.
Energy Storage and Grid Integration: The integration of steam turbines with energy storage devices and cutting-edge grid technologies will help shift to a more adaptable and durable energy grid.
To sum up, steam turbines remain a vital component of the global energy sector, providing dependable and effective power production solutions for a variety of uses. Steam turbines will continue to be a crucial part of the energy mix as technology develops and the energy environment changes, helping to create a more robust and sustainable energy future.
New Materials in Steam Turbine Construction
New materials must be developed to increase steam turbines' longevity, dependability, and efficiency. Thanks to developments in materials science, steam turbines can now run at higher temperatures and pressures, improving their overall performance and lowering maintenance needs. This section examines the most recent developments in turbine materials, their advantages, and the difficulties in implementing them.
High-Temperature Alloys
High-temperature alloys are necessary for parts of steam turbines that are subjected to harsh environments. These materials must retain their mechanical strength and resistance to deterioration while withstanding high temperatures, pressures, and corrosive conditions.
Nickel-Based Superalloys: Because of their remarkable high-temperature strength and resilience to corrosion, oxidation, and creep, nickel-based superalloys are frequently found in steam turbine rotors and blades. These alloys provide more effective energy conversion since they can function at temperatures higher than 700°C (1292°F). Recent developments have concentrated on improving these alloys' composition and microstructure in order to improve their performance further. Superalloys based on nickel include Nimonic 263, René 80, and Inconel 718.
Cobalt-Based Superalloys: These superalloys are utilized in components where thermal cycling is an issue because of their exceptional resistance to thermal fatigue. They are frequently used in situations with a high sulfur content and provide good corrosion resistance. In some turbine applications, cobalt-based alloys such as FSX-414 and Haynes 188 are commonly used.
Titanium Alloys: Because of their high strength-to-weight ratio, titanium alloys are prized for being appropriate for low-pressure turbine blades and other parts where weight reduction is crucial. Applications requiring both mechanical strength and corrosion resistance employ titanium alloys like Ti-6Al-4V. The characteristics of titanium alloys have been enhanced by advancements in processing methods, such as powder metallurgy, making them more competitive with conventional materials.
Ceramic and Composite Materials
Because of their special qualities—such as their tolerance to high temperatures, low density, and superior thermal insulation—ceramic and composite materials are being investigated for application in steam turbines. These materials have the potential to improve environmental impact and efficiency.
Ceramic Matrix Composites (CMCs): CMCs are lightweight materials that are appropriate for hot-section components such as turbine blades since they can tolerate very high temperatures. They are lighter than conventional metal alloys and have better corrosion resistance and thermal stability. CMCs, like silicon carbide (SiC) and alumina-based composites, are being utilized to raise the working temperature of steam turbines, increasing their efficiency.
Silicon Carbide (SiC) Ceramics: Ceramics made of silicon carbide (SiC) are renowned for their exceptional wear resistance, low thermal expansion, and strong heat conductivity. They are employed in turbine parts where robustness and thermal stability are essential, including nozzles and seals. Complex SiC ceramic components with enhanced characteristics may now be produced because of advancements in manufacturing techniques like chemical vapor infiltration.
Glass and Carbon Fiber Composites: These materials are used to improve thermal insulation and reduce weight in non-load-bearing parts like coverings and casings. By altering the resin matrix and fiber orientation, these materials may be customized for particular uses and provide excellent strength-to-weight ratios.
Coatings and Surface Treatments
Surface treatments and coatings are essential for improving the longevity and performance of steam turbine parts. They increase overall dependability and efficiency by offering defense against erosion, corrosion, and heat deterioration.
Thermal Barrier Coatings (TBCs): The application of Thermal Barrier Coatings (TBCs) on turbine blades and vanes protects the underlying metal from high temperatures, enabling higher operating temperatures and increased efficiency. A ceramic layer, like yttria-stabilized zirconia (YSZ), which offers thermal insulation, and a metallic bond coat, which improves adhesion and guards against oxidation, are the usual components of these coatings. In order to allow turbines to run at even greater temperatures, recent advancements in TBC technology have concentrated on improving the thermal stability and endurance of these coatings.
Erosion and Corrosion-Resistant Coatings: By shielding turbine parts from deterioration and chemical assault, these coatings increase their lifespan and lower maintenance needs. Techniques including heat spraying, physical vapor deposition (PVD), or chemical vapor deposition (CVD) are commonly used to apply these coatings. Improvements in nanostructured coatings have increased their efficacy and provided better defense against harsh conditions.
Coatings that are resistant to oxidation: These coatings shield metal parts from oxidation at high temperatures, which can cause failure and material deterioration. These coatings frequently consist of layers of aluminide or platinum-aluminide that create a protective oxide scale on the exterior. To increase component lifespans and oxidation resistance, researchers are investigating novel coating compositions and application techniques.
Challenges and Considerations
Although new materials have many benefits for steam turbines, there are a number of issues and concerns to take into account when using them.
Cost and Availability: Superalloys and CMCs are examples of advanced materials that can be costly and may need specific manufacturing techniques. A crucial factor in turbine design and manufacturing is striking a balance between material performance and cost-effectiveness.
Manufacturing and Fabrication: Advanced manufacturing processes like precision casting and additive manufacturing are necessary to fabricate intricate turbine components out of novel materials. Reliable turbine operation depends on consistent and high-quality material characteristics and component dimensions.
Compatibility and Integration: Changing component geometry and assembly techniques may be necessary to incorporate new materials into turbine designs that already exist. To prevent problems like galvanic corrosion and thermal expansion mismatch, compatibility with other materials and systems, like cooling and lubrication, must be properly assessed.
Testing and Validation: Extensive testing and validation are required to ensure that new materials satisfy the performance and dependability criteria of steam turbines. This involves assessing the characteristics of the material under mimicked working conditions, such as high pressures, temperatures, and cyclic loads.
Conclusion
The creation of novel materials is fueling significant improvements in steam turbine performance, efficiency, and dependability. By allowing turbines to function at higher temperatures and pressures, high-temperature alloys, ceramics, composites, and sophisticated coatings are increasing energy conversion efficiency and lessening their negative effects on the environment. These materials will be essential in determining the direction of steam turbine technology as research and development proceed, helping to create a more efficient and sustainable energy environment.
Improvements in Steam Turbine Lifespan
Because it directly affects the dependability, effectiveness, and overall cost-effectiveness of power generation systems, extending the lifespan of steam turbines is an essential component of modern engineering. Advancements in technology, design, materials, and maintenance procedures have extended the operational life of steam turbines. With an emphasis on the main elements that lead to extended turbine lifespans, this section delves deeply into these advancements.
Optimizing the operational and financial performance of power generation systems requires extending the life of steam turbines. Developments in technology, materials, design, and maintenance procedures have increased steam turbines' lifetime and dependability. This section examines the main tactics and developments that extend turbine lifespan.
Advanced Materials and Coatings
The application of cutting-edge materials and coatings significantly extends the life of steam turbines by strengthening their resistance to high temperatures, corrosion, erosion, and mechanical loads.
High-Temperature Alloys: The invention of high-temperature alloys, such as titanium alloys and nickel-based superalloys, has greatly increased the endurance of turbine components. These materials' exceptional mechanical strength, creep resistance, and corrosion resistance at high temperatures allow turbines to run more effectively and dependably for longer.
Ceramic matrix composites (CMCs): Because of their exceptional thermal stability and resistance to corrosion and wear, CMCs are being utilized more and more in hot-section components and turbine blades. Critical turbine elements have a longer lifespan because of CMCs, which lessen the thermal stresses that metal components endure.
Advanced Coatings: To shield turbine components from mechanical wear and environmental damage, protective coatings such as thermal barrier coatings (TBCs), erosion-resistant coatings, and anti-corrosion coatings are used. These coatings prolong component lifespans and slow down material deterioration, which prolongs turbine operation and lowers maintenance expenses.
Design Optimization
Design innovations have concentrated on lowering mechanical stresses, increasing thermal efficiency, and boosting overall turbine durability to extend turbine lifespans.
Optimized Blade Design: Thanks to developments in computational fluid dynamics (CFD) and computer-aided design (CAD), engineers may now optimize blade shapes for better aerodynamic efficiency and lower mechanical stresses. Optimized blades have a longer service life because they are less worn and fatigued.
Cooling Technologies: By lowering thermal stress and prolonging the life of vital components, efficient cooling systems, like steam-cooled and air-cooled designs, help control the heat load on turbine components. By keeping parts operating within safe temperature ranges, these cooling systems guard against overheating and material deterioration.
Control of Vibration: Resonance and vibration can cause mechanical wear and tear and turbine component failure. Improved balancing and damping systems are two design techniques that reduce vibration and increase the longevity and dependability of steam turbines.
Stress-Relief Techniques: Design changes that lessen stress concentrations, such as rounded corners and seamless transitions in component geometries, help halt the start and spread of cracks. These stress-relieving methods also increase the operational life of turbine components and enhance their durability.
Enhanced Maintenance Practices
Routine maintenance and observation are essential for steam turbines to operate reliably and efficiently over the long term. Improvements in maintenance procedures result in longer turbine lifespans.
Predictive Maintenance: By using techniques like vibration analysis, thermal imaging, and condition monitoring, operators can identify any problems before they become serious. Predictive maintenance allows for prompt interventions and avoids expensive breakdowns by seeing wear, corrosion, or mechanical stress early.
Frequent Inspections and service: Planned inspections and services guarantee that turbine parts are in good shape and functioning within predetermined bounds. Cleaning, lubrication, and calibration are examples of routine maintenance procedures that help turbine components operate at their best and last longer.
Component Replacement and Refurbishment: To increase a turbine's lifespan, worn-out or damaged components must be replaced and refurbished. By renewing key parts, such as blades, rotors, and bearings, operators can restore turbine performance and prevent further degradation.
Expertise and Operator Training: The efficient operation of steam turbines depends on skilled operators and maintenance staff. Thorough training courses and access to technical know-how guarantee that turbines are maintained and operated properly, lowering the chance of malfunctions and increasing longevity.
Technological Innovations
Recent advancements in technology have increased steam turbines' lifespan by improving their dependability, efficiency, and performance.
Digital Twin Technology: Digital twins, virtual representations of actual turbines, make real-time monitoring, simulation, and analysis possible. They provide predictive maintenance and optimization techniques by offering comprehensive information on turbine health and performance, hence increasing turbine lifespan.
Advanced Control Systems: Automated control systems driven by machine learning and artificial intelligence algorithms maximize turbine performance by modifying parameters in response to shifting conditions. These systems' increased performance, lower emissions, and increased efficiency result in longer turbine lifespans.
Remote Monitoring and Diagnostics: Remote monitoring and diagnostics capabilities enable operators to monitor turbine performance from a central location, improving operational efficiency and prompt problem-solving. This technique is especially useful for overseeing sizable turbine fleets spread over several places.
Energy Management Systems: When combined with other power generation assets like gas turbines and renewable energy sources, advanced energy management systems maximize the performance of steam turbines. These systems increase overall efficiency and prolong the life of turbine components by balancing energy production and consumption.
Case Studies and Success Stories
Analyzing actual turbine lifespan enhancements can yield important information about the best methods and approaches for prolonging steam turbine life.
Combined Cycle Power Plant Optimization: A combined cycle power plant uses digital twin technology, sophisticated coatings, and predictive maintenance methods as part of a thorough maintenance and optimization program. As a result, the plant's steam turbines' lifespan increased by 30%, decreasing maintenance expenses and increasing overall efficiency.
Erosion Mitigation for Geothermal Plants: Because of corrosive impurities and abrasive particles in the steam, a geothermal power plant had to deal with erosion and corrosion. The factory greatly increased the lifespan of its turbine components, improving performance and dependability by applying erosion-resistant coatings and streamlining the chemistry of steam.
Refurbishment of Nuclear Power Plant Components: After a thorough investigation of its steam turbine components, a nuclear power plant identified important areas needing replacement and refurbishment. The factory increased the lifespan of its turbines and enhanced safety and efficiency by replacing important parts and applying cutting-edge materials and coatings.
Conclusion
Increasing the lifespan of steam turbines is a complex task that calls for improvements in technology, materials, design, and maintenance procedures. Engineers may greatly increase the operational life of steam turbines, enhancing their dependability, efficacy, and economy by utilizing high-temperature alloys, ceramic composites, sophisticated coatings, and digital technology. Further advancements in turbine technology and materials will be essential to attaining a more efficient and sustainable energy future as research and development proceed.
Turbine Efficiency Gains
In power generation, increasing the efficiency of steam turbines is a top priority because even modest improvements can result in notable decreases in fuel consumption and greenhouse gas emissions. The efficiency of steam turbines has significantly increased over time due to developments in materials, design, and technology. This section examines the numerous developments and contributing factors that have increased steam turbine efficiency.
Steam turbine efficiency is essential to maximizing power generation and minimizing environmental impact. Developments in design, materials, technology, and operating procedures have made significant improvements in steam turbine efficiency possible. This section examines the main ideas and elements influencing these advancements.
Thermodynamic Principles and Efficiency
Thermodynamic principles, which mainly concentrate on transforming thermal energy into mechanical work, control the efficiency of steam turbines. Heat addition, expansion, heat rejection, and compression are the steps in the Rankine cycle that form the foundation of steam turbine functioning. Optimizing these steps can increase a steam turbine's efficiency.
Greater Steam Temperatures and Pressures: Running at greater steam temperatures and pressures is one of the best strategies to boost turbine efficiency. Higher steam conditions allow for increased energy extraction by increasing the thermal energy available for conversion. With an efficiency of over 45%, contemporary supercritical and ultra-supercritical turbines run at temperatures above 600°C and pressures higher than the critical point of water (22.1 MPa).
Reheat and Regenerative Cycles: By reducing energy losses, the application of reheat and regenerative cycles can increase turbine efficiency. Steam is partially expanded in the turbine, reheated in a boiler, and then expanded once more in a subsequent turbine stage in a reheat cycle. Raising the average temperature at which heat is applied improves efficiency. Regenerative cycles recover waste heat and use less fuel by preheating the water before it enters the boiler using feedwater heaters.
Advanced Thermodynamic Cycles: Efficiency improvements have also been facilitated by advancements in thermodynamic cycles, such as the combined cycle and organic Rankine cycle (ORC). Gas turbines and steam turbines are integrated into combined cycle power plants, which increase overall efficiency by producing steam from gas turbine waste heat. Because organic fluids have lower boiling points than water, ORC systems can convert low-temperature heat sources into energy efficiently.
Advanced Materials and Blade Design
The efficiency of steam turbines has increased significantly as a result of the creation of cutting-edge materials and improved blade designs.
High-Temperature Materials: By enabling turbines to function at greater temperatures and pressures, high-temperature materials—such as ceramic matrix composites (CMCs) and nickel-based superalloys—improve thermal efficiency. Because of their superior strength, resistance to corrosion, and thermal stability, these materials allow for more effective energy conversion.
Aerodynamic Blade Design: Blade shapes can now be optimized for better aerodynamic performance due to developments in computer-aided design (CAD) and computational fluid dynamics (CFD). Modern turbine blades are made to maximize energy extraction and minimize aerodynamic losses to reduce turbulence and increase efficiency. Techniques like curved end walls and 3D blading improve aerodynamic performance even more.
Tip Clearance Control: Minimizing the tip clearance between the turbine blades and the casing increases efficiency and decreases aerodynamic losses. Modern tip clearance control techniques, like abradable coatings and active clearance control, aid in preserving ideal clearances and minimizing leakage losses.
Surface treatments and blade coatings: By applying cutting-edge coatings and surface treatments to turbine blades, their resistance to erosion, corrosion, and thermal deterioration is increased, increasing their lifespan and efficiency. Erosion-resistant coatings and thermal barrier coatings (TBCs) support the preservation of blade performance and integrity.
Digitalization and Control Systems
Steam turbine efficiency and operation have changed as a result of digitalization and sophisticated control systems.
Real-Time Diagnostics and Monitoring: Cutting-edge sensors and monitoring systems offer up-to-date information on critical turbine characteristics, including vibration, pressure, and temperature. Operators can use this data to maximize turbine efficiency and performance, identify possible problems early, and take corrective action.
Automated Control Systems: Computerized control systems, powered by artificial intelligence and machine learning algorithms, optimize turbine operation by modifying parameters in response to shifting conditions. These systems increase overall performance, lower emissions, and boost efficiency.
Digital Twins: Digital twin technology allows for the creation of virtual models of actual turbines, making real-time simulation and analysis possible. This technology also allows for predictive maintenance and optimization techniques, increasing dependability and efficiency.
Predictive Maintenance: By using methods like vibration analysis and condition monitoring, predictive maintenance helps find possible problems before they become serious. Better turbine efficiency and less downtime are two benefits of predictive maintenance, which makes it possible to make timely interventions and optimize maintenance plans.
Operational Strategies and Best Practices
In order to maximize the efficiency of steam turbines, operational strategies and best practices are essential.
Optimizing load: Running turbines at ideal load levels guarantees maximum effectiveness and reduces energy loss. Thanks to sophisticated control systems and real-time monitoring, operators can maximize efficiency by modifying turbine output in response to demand.
Starting and Shutdown processes: Effective starting and shutdown processes improve efficiency and lessen wear on turbine components by minimizing energy losses and thermal stress. These processes are automated by sophisticated control systems, guaranteeing reliable and efficient operation.
Fuel and Steam Purity: For turbines to operate efficiently, high fuel and steam purity must be maintained. Fuel and steam impurities have the potential to reduce efficiency and increase maintenance needs by causing fouling, corrosion, and erosion. For best results, fuel and steam should be regularly monitored and treated.
Waste Heat Recovery: Energy from exhaust gases and other heat sources is recovered by installing waste heat recovery devices, including heat exchangers and economizers. This increases plant efficiency overall. Cogeneration systems and combined cycle power plants are two instances of efficient waste heat recovery.
Case Studies and Success Stories
Examples of efficiency gains from the real world offer important insights into the best methods and approaches for raising steam turbine efficiency.
Efficiency Gains in Ultra-Supercritical Power Plants: By utilizing cutting-edge materials, optimized blade designs, and digital control systems, an ultra-supercritical power plant was able to attain efficiencies of more than 47%. Running at high temperatures and pressures, the plant maximized energy output while minimizing pollution and fuel consumption.
Combined Cycle Plant Optimization: To increase efficiency, a combined cycle power plant coupled waste heat recovery methods with sophisticated monitoring and control systems. The facility demonstrated the promise of combined cycle technology for efficient power generation by achieving total efficiencies of over 60%.
Enhancement of Geothermal Plant Efficiency: To increase efficiency, a geothermal power plant used cutting-edge blade coatings and organic Rankine cycle (ORC) technologies. The facility enhanced energy output and decreased operating expenses by employing low-temperature heat sources and reducing energy losses.
Conclusion
Improving steam turbine efficiency is a complex task that calls for improvements in design, technology, materials, and operating procedures. Through the use of high-temperature materials, better blade designs, digitalization, and sophisticated control systems, engineers have significantly increased the efficiency of steam turbines, lowering fuel consumption and their negative environmental effects. Further advancements in turbine technology will be essential to attaining a more efficient and sustainable energy future as research and development proceed.
Components of a Steam Turbine and Their Manufacturing
Each element of the intricate machines known as steam turbines is essential to the process of turning steam energy into mechanical work. Gaining knowledge of the parts and how they are made can help one better understand the engineering and technology used in the production of steam turbines.
Rotor
Description
The central shaft of the steam turbine, to which the turbine blades are fastened, is called the rotor. It is an essential part that transfers the rotating motion to the generator or mechanical load and transforms steam energy into mechanical energy.
Manufacturing Process
Material Selection: High-strength, low-alloy steels, such as chromium-molybdenum-vanadium (CrMoV) alloys, which provide superior mechanical qualities and resilience to heat stresses, are commonly used to make rotors.
Forging: A big billet of steel is heated to high temperatures and formed into a rough form using a hydraulic press or hammer in the hot forging process, which is often used to manufacture the rotor. This procedure improves the material's strength and hardness while aligning the grain structure.
Machining: Following forging, the rotor is subjected to precision machining to obtain the required dimensions and surface polish. The rotor is milled, turned, and ground to precise specifications using computer numerical control (CNC) machinery. Machining procedures guarantee tight tolerances and balance, which are essential for reducing vibration and increasing productivity.
Heat Treatment: To improve its mechanical qualities, the rotor undergoes heat treatment procedures such as quenching and tempering. Heat treatment enhances the rotor's strength, durability, and resistance to wear and creep.
Balance: Dynamic balancing guarantees that the rotor runs smoothly at high speeds without producing undue vibration. Balancing involves adding or withdrawing material from the rotor to achieve an equitable distribution of weight.
Inspection and Testing: To find any flaws or irregularities, the rotor is thoroughly inspected and tested, including non-destructive testing (NDT) methods like magnetic particle inspection and ultrasonic testing.
Blades
Description
Components that resemble airfoils, known as turbine blades, take energy from steam and transform it into a rotating motion. They are essential to the steam turbine's functionality and efficiency.
Manufacturing Process
Material Selection: Blades are commonly made from high-performance materials like titanium alloys or superalloys based on nickel. These materials provide excellent resistance to mechanical loads, corrosion, and high temperatures.
Precision Casting: Turbine blades are frequently made via investment casting, sometimes referred to as lost-wax casting. In this procedure, a wax model of the blade is made, coated with a ceramic material to create a mold, and the wax is melted away. The blade is formed by pouring molten metal into the mold.
Directional Solidification: Advanced casting techniques, including directional solidification and single-crystal growth, are employed to improve the mechanical characteristics of turbine blades. By regulating the material's grain structure, these methods increase the material's resistance to fatigue and creep.
Machining and Finishing: Following casting, blades undergo precise machining and finishing procedures to obtain the required form and surface quality. The blades are milled and ground to exact specifications using CNC equipment.
Application of Coating: Blades are covered with protective coatings, such as erosion-resistant coatings and thermal barrier coatings (TBCs), to improve their performance and longevity. Techniques include chemical vapor deposition (CVD) and thermal spraying.
Inspection and Testing: Blades are subjected to stringent inspection and testing, including non-destructive testing techniques, to ensure they fulfill quality and performance requirements. Defects are frequently found using ultrasonic testing and high-resolution imaging.
Casing
Description
The steam turbine is enclosed by the casing, also known as the housing, which offers structural support. It guides the steam's passage through the turbine's stages and aids in regulating temperature and pressure.
Manufacturing Process
Material Selection: Cast steel or ductile iron, which provide a good blend of strength, toughness, and thermal resistance, are commonly used to make casings.
Casting: The casing is often constructed via sand casting, in which a mold is created by packing sand around a wooden or metal casing design. The case is made by pouring molten metal into the mold.
Machining: After casting, the case is machined to obtain the necessary dimensions and tolerances. Flanges, apertures, and mounting surfaces are machined using CNC machines.
Heat Treatment: Annealing and other heat treatment procedures reduce internal tensions and enhance the casing's mechanical qualities.
Welding and Assembly: Large casings may consist of several pieces joined via welding. Non-destructive testing techniques examine welds and guarantee their integrity and quality.
Inspection and Testing: Casings are subjected to inspection and testing, which includes pressure testing and dimensional checks, to ensure they fulfill performance and safety requirements.
Bearings
Description
The rotor is supported by bearings, which enable smooth, low-friction rotation. They are essential for preserving the turbine shaft's stability and alignment.
Manufacturing Process
Material Selection: High-strength steel, ceramics, or babbitt, a soft metal alloy, are common materials used to make bearings. The particular application and operating conditions determine the choice of material.
Precision Machining: Precision machining techniques produce smooth surfaces and strict tolerances in bearings. The rolling components and bearing races are machined using CNC machines.
Heat Treatment: Heat treatment techniques, such as case hardening, improve the fatigue strength and wear resistance of bearing components.
Assembly and Inspection: Bearings are assembled using rolling components like balls or rollers and then tested and inspected to guarantee correct fit and operation.
Lubrication System Integration: Lubrication systems are integrated with bearings to lessen wear and friction. They provide the bearing surfaces with a steady flow of lubricant.
Governor
Description
The governor is a control device that manages the steam turbine's speed and output by modifying the steam flow. It guarantees that the turbine runs within safe and effective bounds.
Manufacturing Process
Fabrication of Components: The governor consists of several parts, including actuators, linkages, and valves, all of which are produced using precision machining and fabrication methods.
Assembly: The parts come together to form the governor mechanism, which reacts to variations in load and turbine speed.
Testing and Calibration: The governor is calibrated to guarantee precise and dependable management of the turbine speed and output. Operating situations are simulated to test the governor's performance.
Integration with Control Systems: To maximize performance and efficiency, the governor is integrated with the turbine's control systems, which may include sensors and digital controllers.
Nozzles
Description
In impulse turbines, high-velocity steam jets directed onto the turbine blades via nozzles add momentum and rotate the turbine.
Manufacturing Process
Material Selection: Nozzles are commonly made from high-strength alloys, including stainless steel or superalloys based on nickel, that can tolerate high temperatures and pressures.
Precision Machining: To obtain the required form and flow properties, nozzles are made using precision machining processes. CNC machines shape, mill, and drill the nozzle passages.
Heat Treatment: Annealing and quenching are examples of heat treatment procedures that are used to improve the nozzles' mechanical characteristics.
Application of Coating: Protective coatings may be applied to improve nozzles' resistance to corrosion and erosion.
Inspection and Testing: To make sure they fulfill performance requirements, nozzles are subjected to inspection and testing, which includes dimensional inspections and flow testing.
Seals and Gaskets
Description
Seals and gaskets keep the turbine's pressure differentials constant and stop steam leakage. They are essential for effective functioning and loss prevention.
Manufacturing Process
Material Selection: Materials with superior sealing qualities and resilience to high temperatures and pressures are used to make gaskets and seals. Metal alloys, graphite, and elastomers are examples of common materials.
Molding and Cutting: Depending on the material and design, seals and gaskets are created using either molding or cutting techniques. Metal gaskets are cut from sheets, whereas rubber and elastomeric seals are usually molded.
Coating and Treatment: Seals and gaskets may be treated with surface treatments, such as coatings or impregnations, to improve their longevity and sealing capabilities.
Inspection and Testing: Seals and gaskets are examined and tested for dimensional accuracy and sealing effectiveness to ensure they fulfill quality standards.
Conclusion
Advanced materials, precise engineering, and strict quality control are used in the production of steam turbine components to guarantee peak performance, dependability, and efficiency. Every part is essential to the turbine's overall functioning, and developments in manufacturing techniques and materials keep pushing turbine technology forward. A more sustainable and effective energy future will be facilitated by additional advancements in the production of turbine components as
research and development continue.
Generator:
A generator is a machine that uses electromagnetic induction to transform mechanical energy into electrical energy. In the context of power generation, generators are essential for converting the rotational motion created by different prime movers into electrical power.
A generator rotor revolves inside a magnetic field and is frequently attached to an engine or turbine. Using electromagnetic induction, this rotating motion creates an electromotive force (EMF) in the rotor's conductors. An external circuit then conducts the electrical current that results from the generator.
Generators are crucial parts of power plants, from small-scale applications to large-scale utility plants. To generate power, they are frequently connected to internal combustion engines, gas turbines, water turbines, or steam turbines. Asynchronous generators (induction generators) and synchronous generators are two typical types of generators, but there are other options as well.
Synchronous generators ensure steady and coordinated power generation by staying in sync with the electrical grid's frequency. Induction generators, sometimes referred to as asynchronous generators, are frequently employed in renewable energy systems since they do not require grid synchronization.
Generators are essential for delivering a steady and dependable source of electrical power for various uses, such as industrial operations, home electricity supply, and the larger electric grid. As power production systems evolve generally, ongoing developments in generator technology seek to increase efficiency, dependability, and the integration of generators with new energy sources.
Coupling: A generator's rotor is attached to the steam turbine's revolving shaft.
Principle: Electromagnetic induction transforms spinning motion into electrical energy.
Power Generation:
The process of turning different types of energy into electrical power is known as power generation. This vital operation produces the Electricity required for commercial, industrial, and household uses. Other technologies and energy sources can be used in various ways to generate power. This is a summary without numbers:
Power generation involves the transformation of energy into Electricity. Various methods are employed, each relying on different energy sources and technologies. The key components and processes in power generation include:
Energy Sources:
Fossil Fuels: The burning of oil, coal, and natural gas in thermal power plants.
Nuclear: Using nuclear reactions to produce steam turbine heat.
Renewable Energy: Utilizing energy from renewable sources such as biomass, wind, water (tidal and hydroelectric), and sunlight.
Power Plants:
Thermal Power Plants: These facilities use heat from nuclear reactors or the burning of fossil fuels to create steam, which powers turbines.
Hydroelectric Power Plants: Use the water's kinetic energy to drive turbines.
Wind Power Plants: Wind turbines are used to transform the kinetic energy of the wind into mechanical energy.
Solar Power Plants: Utilize photovoltaic cells or systems that use concentrated solar energy to capture sunlight.
Biomass Power Plants: Produce energy by burning organic materials or by biological processes.
Turbines:
Steam Turbines: High-pressure steam generated in boilers powers steam turbines.
Gas Turbines: Direct turbine rotation is achieved by using combustion gasses.
Water turbines: In hydroelectric power facilities, these are rotated by the flow of water.
Generators:
The process of electromagnetic induction converts mechanical energy into electrical energy.
Synchronous and asynchronous generators are among the varieties.
Transmission and Distribution:
A power line system is used to transport Electricity from power facilities to final consumers.
Transformers modify voltage to ensure effective distribution and transmission.
Control Systems and Automation:
For safe and effective operation, keep an eye on and manage a number of aspects.
For grid stability and optimal energy production, automate processes.
Environmental Considerations:
Emission Control: Use technology to reduce the impact on the environment, particularly in power plants that rely on fossil fuels.
Renewable Integration: To lessen carbon emissions, raise the proportion of renewable energy.
Grid Connection:
Connect power plants to the electrical grid to ensure a steady and dependable supply of energy.
To keep the grid stable, balance the supply and demand for Electricity.
With continuous technological breakthroughs and an increasing focus on sustainability, power generation is a dynamic subject. Power generation techniques are evolving to improve efficiency, lessen the impact on the environment, and guarantee a steady supply of energy in the future.
Output: Alternating current (AC) is the electrical power produced by the generator.
Frequency: Depending on the area, the AC power frequency is normally 50 or 60 Hz.
Condenser:
In a power plant's steam cycle, a condenser is an essential part that helps turn steam back into liquid water after it has passed through a steam turbine. This procedure is required to maintain the power-producing system's efficiency.
A condenser's main job is to release latent heat from the turbine's steam, turning it into liquid water. It is usually found at the steam turbine's exhaust end. Following its passage through the turbine blades, the steam enters the condenser and encounters tubes or surfaces that an external medium has cooled. This cooling medium may be air in the case of air-cooled condensers or water from a river, the sea, or a cooling tower.
When the heat exchange process releases its latent heat, steam condenses into water. This heat is absorbed by the cooling medium and transferred out of the condenser. The location and architecture of the power plant influence the selection of cooling mediums. Condensed water is frequently used as feedwater in the steam cycle, and water is a typical cooling medium.
Maintaining a vacuum inside the condenser is essential to increasing the steam turbine's efficiency, enabling the steam to expand further, and extracting more work.
Condensers come in various forms, such as surface condensers, which condense steam on the surface of tubes, and jet condensers, which condense steam by coming into direct contact with a cooling water jet.
Routine maintenance is necessary to guarantee optimal condenser operation. Common maintenance tasks include cleaning tubes, checking for leaks, and dealing with corrosion.
The environmental impact of condenser discharges is minimized, especially when water is used as a cooling medium. Environmental rules and technologies like cooling towers are intended to address these issues.
In conclusion, a condenser is an essential part of a power plant's steam cycle. It helps the steam turbine run efficiently by turning spent steam back into liquid water that can be used in the boiler.
Function: Water is condensed from steam as it leaves the turbine.
Heat Transfer: A cooling medium receives the latent heat that is emitted during condensation.
Cooling Medium: Depending on the type of power plant, either air or water is typically used.
Cooling System:
Cooling Tower: In certain situations, a cooling tower evaporates water and releases extra heat into the atmosphere.
Water Source: Lakes, rivers, or the ocean may provide the cooling water.
Control Systems:
Automation: Modern power plants employ sophisticated control systems to regulate a number of characteristics.
Safety precautions: Mechanisms are in place to guarantee secure functioning and handle crises.
Efficiency Considerations:
Thermal Efficiency: Several variables, including heat exchanger efficiency, steam characteristics, and turbine design, affect the system's overall efficiency.
Cogeneration: By repurposing waste heat for other uses, such as district heating, some power facilities employ cogeneration to increase efficiency.
Environmental Impact:
Emissions Control: Fossil fuel-based power plants frequently install emissions control systems to lessen their influence on the environment.
Integration of Renewable Energy: Using renewable energy helps reduce carbon emissions.
Maintenance and Upkeep:
Frequent Maintenance: To guarantee the equipment's longevity and dependability, scheduled maintenance is essential.
Upgrades: Power plants may undergo upgrades to address environmental issues or integrate more efficient technologies.
Knowing these specifics helps one better understand the intricate interactions between the various parts and procedures that go into producing Electricity with steam power. The ongoing development of technology seeks to improve productivity, lessen its negative effects on the environment, and investigate novel methods of producing Electricity.
Steam Turbines
Steam turbines are vital to many industrial operations and contemporary electricity generation. They transform steam's thermal energy into mechanical energy, which can power machinery or produce Electricity. The idea of using steam power has existed since antiquity. Hero of Alexandria created the Aeolipile, a basic steam-powered device, in the first century AD as an early attempt to use steam for mechanical purposes. However, steam turbines as we know them today didn't start to take shape until the 19th Century.
The late 19th Century saw the development of steam turbine technology thanks to the efforts of Gustaf de Laval and Sir Charles Parsons. When Sir Charles Parsons created a prototype in 1884 that could power an electrical generator, he was frequently given credit for making the modern steam turbine. This technology was far more efficient than previous steam engines. Modern turbines still retain the design concepts of Parsons' steam turbine, which swiftly emerged as the most popular way to produce power.
Swedish engineer Gustaf de Laval greatly aided the development of steam turbines, especially high-speed turbines. His efforts during the 1880s and 1890s resulted in the development of impulse turbines, which powered their blades using the kinetic energy of steam. These advancements made the broad use of steam turbines across numerous sectors possible.
Importance in Modern Industry
These days, steam turbines are essential to the world's energy system. They produce a sizable amount of the Electricity produced worldwide in thermal power plants. In a conventional thermal power plant, steam is generated either by using nuclear energy or by burning fossil fuels like coal, natural gas, or oil. After entering the turbine, the steam transforms thermal energy into mechanical energy by expanding and propelling the turbine blades. Electricity is then produced by rotating an electrical generator using this mechanical energy.
Additionally, steam turbines are essential to many industrial operations. They power pumps and compressors in the petrochemical sector, mechanical drives in the steel sector, and energy generation and machinery powering the paper sector. The dependability and efficiency of steam turbines are also highly prized in maritime propulsion systems, especially in big warships like aircraft carriers and submarines.
Due to their adaptability and efficiency, steam turbines are essential in both conventional and contemporary energy systems. Fossil fuels, nuclear power, and renewable energy sources, including biomass, geothermal, and concentrated solar power, are all compatible with them. Because of their versatility, steam turbines will remain an essential part of the world's energy mix as it moves toward more environmentally friendly energy sources.
Fundamentals of Steam Turbines
Basic Principles
The fundamental function of a steam turbine is to transform steam's thermal energy into mechanical energy. The Rankine cycle, the basic thermodynamic cycle utilized in steam turbine operations, serves as the foundation for this procedure, which is based on the laws of thermodynamics.
To put it simply, there are four primary processes involved in the Rankine cycle:
Heat Addition: Water is heated at a steady pressure in a boiler to produce steam. There is a lot of thermal energy in this high-pressure steam.
Expansion: After being driven into the turbine, the high-energy steam expands. The turbine blades rotate as a result of the expansion of the steam, which also lowers the temperature and pressure. A shaft that is attached to a mechanical device or electrical generator receives this rotational energy.
Condensation: The steam is cooled and condensed back into water in a condenser after coming from the turbine.
Pumping: To restart the cycle, the condensed water is subsequently pumped back into the boiler.
A measure of a steam turbine's efficiency is how well it transforms the thermal energy in the steam into mechanical energy. Variables, including temperature, steam pressure, and turbine blade design, mostly determine this efficiency.
Key Components
A number of essential parts make up steam turbines, and each one is vital to the turbine's functioning:
Rotor: The turbine's revolving component, the rotor, consists of a shaft and associated blades. Steam transforms thermal energy into mechanical energy by spinning the rotor as it moves through the turbine.
Stator: The stator is the stationary component of the turbine that encircles the rotor. It has fixed blades that efficiently guide the steam flow onto the rotor blades.
Casing: The casing surrounds the entire turbine, supporting it structurally and keeping the steam inside. Additionally, it shields the internal parts from the elements.
Blades: The turbine's blades are essential to energy conversion. Blades come in two primary varieties: moving blades attached to the rotor and fixed blades fastened to the stator. The blades' layout and design are essential to the turbine's effective functioning.
Steam Supply System: This system consists of the pipes, valves, and other parts that supply the turbine with steam at the proper temperature and pressure. It also regulates how much steam enters the turbine.
Condenser: The turbine's exhaust steam is cooled by the condenser, which then turns it back into water for the cycle's reuse. Usually, a heat exchanger is used to extract the steam's latent heat of vaporization.
Governor: The governor is a control device that modifies the steam flow to alter the turbine's speed. It guarantees that the turbine can react to variations in load demand and run at the intended speed.
The design, mechanism of steam expansion, and application of steam turbines determine their classification. Among the primary kinds are:
Impulse Turbines: These turbines use nozzles to deliver high-pressure steam onto the turbine blades. The blades move as a result of the steam jets striking them, but the steam pressure stays constant while it passes over the blades. The steam's impulse force is the only source of motion for the rotor. Impulse turbines can be used to drive generators in power plants and are frequently employed in high-speed applications.
Reaction Turbines: In contrast to impulse turbines, reaction turbines make use of both the steam's impulse and the reaction force produced when the steam accelerates and expands through the rotating blades. The rotor is propelled by the pressure decrease that occurs as the steam moves through the blades. Reaction turbines are frequently seen in industrial environments and are utilized in lower-speed applications.
Condensing Turbines: These turbines are made to release steam into a condenser to condense it into water at a lower pressure. When generating electricity and optimum efficiency is needed, condensing turbines are frequently utilized.
Non-Condensing Turbines: Also referred to as back-pressure turbines, these turbines release steam at a pressure greater than atmospheric pressure. The exhaust steam can be used for other industrial processes or heating. Non-condensing turbines are frequently employed in cogeneration systems that require both process steam and power.
Extraction Turbines: These turbines draw steam for heating or industrial processes at one or more locations along the turbine. The residual steam generates power as it passes through the turbine. In applications requiring steam at varying pressures, these turbines offer versatility.
Reheat Turbines: Reheat turbines use a high-pressure stage to expand steam, followed by a lower-pressure stage where the steam is further developed. Reheating increases cycle efficiency and lowers steam moisture content, both of which can lessen blade attrition.
Reheat Turbines: Reheat turbines expand steam first at high pressure and then again at reduced pressure using a second stage. Reheating reduces steam moisture content and improves cycle efficiency, both of which can minimize blade attrition.
Marine Turbines: Designed to be extremely dependable and able to function in harsh sea conditions, marine turbines are found in huge commercial ships and military boats. Reaction turbines are usually used to power generators or propellers for propulsion.
Thermodynamics and Fluid Mechanics
Thermodynamic Cycles
Thermodynamic cycles are the foundation of steam turbine operation, and the Rankine cycle is the most crucial to comprehending how these devices function. The Rankine cycle, a closed-loop cycle that transforms heat into work and is named after William John Macquorn Rankine, is the foundation of steam turbine operations in power plants and industrial settings.
The Cycle of Rankine: There are four primary processes in the Rankine cycle:
Isentropic Compression involves pumping water, the working fluid, from a low pressure to a high pressure. Work input, usually supplied by a pump, is necessary for this operation.
Isobaric Heat Addition: To create high-pressure steam, high-pressure water is heated at a steady pressure in a boiler.
Isentropic Expansion: The turbine's rotor rotates as the high-pressure steam expands inside it. The steam's temperature and pressure decrease as it grows.
Isobaric Heat Rejection: The cycle is finished when the expanding steam condenses back into water at a steady pressure.
Reheating and regenerative feedwater heating are two techniques that can increase the Rankine cycle's efficiency.
Reheat Cycle: This process involves expanding steam in a high-pressure turbine, reheating it in a boiler, and then expanding it once more in a low-pressure turbine. This procedure lowers the moisture content at the turbine's exhaust, which in turn lessens turbine blade attrition and boosts the cycle's thermal efficiency by enabling the steam to expand throughout a wider pressure range.
Regenerative Cycle: The regenerative cycle increases efficiency by using steam collected from different stages of the turbine to preheat the feedwater entering the boiler. This reduces the amount of fuel required to heat the water to the appropriate temperature.
Combined Cycle: This cutting-edge method blends a steam turbine cycle with a gas turbine cycle. A heat recovery steam generator (HRSG) uses the gas turbine's exhaust gases to create steam, which powers a steam turbine. Very high total efficiency is possible with this configuration, frequently above 60%.
Fluid Dynamics in Steam Turbines
Since the effective conversion of steam energy into mechanical work depends on the controlled flow of steam through the turbine, fluid dynamics is essential to the operation of steam turbines.
Steam Flow and Velocity Triangles: Velocity triangles, which are geometric representations of the steam velocity in relation to the turbine blades, define the flow of steam through a turbine. Since steam passes through both stationary (stator) and moving (rotor) blades, these triangles aid in the analysis of the energy conversion process.
Absolute Velocity: The steam's velocity in relation to the turbine's stationary parts.
Relative Velocity: The steam's velocity in relation to the rotor's rotating blades.
Blade Velocity: The speed of motion of the turbine blades.
The degree to which these velocities are optimized to optimize the transmission of energy from the steam to the rotor determines the turbine's efficiency.
Principles of Impulse and Reaction: Steam turbines can function using one of these two concepts or a mix of the two.
Impulse Turbines: Before steam reaches the rotor blades, nozzles expand it, transforming its pressure energy into kinetic energy. The rotor spins because the blades absorb this kinetic energy.
Response Turbines: The steam in a response turbine experiences a pressure decrease as it travels through rotor blades designed to function as nozzles. A reactive force created by the pressure decrease rotates the rotor. Jet engines operate on a similar concept.
The impulse or response design is chosen depending on the particular application; many turbines use both concepts at different phases.
Expansion and Losses: Steam loses energy as it expands through the turbine due to friction, heat loss, and mechanical losses. These losses decrease the turbine's total efficiency. Optimizing turbine performance requires an understanding of and commitment to minimizing these losses.
Frictional losses: Occur as a result of steam rubbing against internal surfaces and turbine blades.
Heat Losses: Occur when steam exchanges heat with the turbine casing or the surrounding air.
Mechanical Losses: Take into account the turbine's bearing, seal, and other mechanical component losses.
To reduce these losses, sophisticated coatings and materials are employed, along with exacting manufacturing processes.
Heat Transfer Mechanisms
Heat transfer is a crucial component of steam turbine operation. It affects performance and efficiency. It involves three main heat transport mechanisms: radiation, convection, and conduction.
Conduction: Heat is transferred by conduction as it passes through solid materials like turbine blades or casing. Conduction is the process by which heat moves from the hot steam to cooler areas through the metal parts of steam turbines. Because it influences the rate of heat transmission and the temperature distribution inside the turbine, the thermal conductivity of the materials used in its construction is a crucial consideration.
Convection: Convection is the transfer of heat from a solid surface to a fluid—in this example, steam. It happens when heat is transmitted from the steam to the turbine blade material as it passes over it. Steam velocity, turbulence, and the blades' surface roughness are some of the variables that affect how efficient this operation is.
Forced Convection: When steam is pushed through a steam turbine at high speeds, forced convection occurs. Optimizing the turbine blade and flow path designs can improve heat transfer via forced convection.
Natural Convection: Although it is less common in steam turbines, natural convection can happen in places where air or steam is stationary. Controlling natural convection is crucial for both structural integrity and turbine cooling.
Radiation: The process by which electromagnetic waves transfer heat. While conduction and convection are usually more important in steam turbines, radiation heat transfer can become substantial at very high temperatures, such as those seen in high-temperature turbines or the superheater sections of a boiler.
Thermal Radiation: Depending on their temperature, the turbine's constituent parts release thermal radiation. If insulation and other thermal management strategies are not used appropriately, this radiation may lead to heat losses.
Effective thermal management in steam turbines requires a careful balancing act between these heat transfer processes to maintain ideal operating temperatures and avoid component overheating, which can result in decreased efficiency or even failure.
Design and Manufacturing of Steam Turbines
Thermodynamic Efficiency: At the start of the design process, thermodynamic calculations are performed to identify the ideal operating parameters, including temperature, flow rate, and steam pressure. Engineers use these computations to ensure that each stage draws the most energy from the steam.
Blade Design: The design of turbine blades greatly influences their efficiency and dependability. Blades must be aerodynamically tuned to maximize energy extraction and minimize losses from friction, turbulence, and separation. To represent the flow of steam through the turbine, computational fluid dynamics (CFD) simulations are frequently used to precisely compute the blades' length, shape, and angle.
Material Selection: High temperatures, high pressures, and mechanical stresses must all be tolerated by the materials used to build turbines. Strength, durability, resistance to erosion and corrosion, and the capacity to continue operating under temperature cycling are the primary criteria that influence the choice of material. Stainless steel, nickel-based superalloys, and high-strength alloys are examples of common materials.
Cooling and Heat Management: Cooling is a crucial design factor in high-temperature turbines, particularly those utilized in power generation. To avoid overheating and preserve structural integrity, blades and other parts are frequently internally cooled with air or steam. In more demanding applications, advanced cooling designs like transpiration cooling or film cooling may be employed.
Rotor Dynamics and Balancing: To guarantee dependable and seamless functioning, the rotor is an essential part that needs to be carefully constructed. To prevent resonance, which could result in mechanical failure, engineers must take into consideration rotor dynamics, including the rotor's inherent frequencies. To avoid excessive vibrations, which can deteriorate bearings and other parts, the rotor must also be carefully balanced.
Sealing and Clearance Control: Reducing steam leakage between the turbine's various stages is crucial to preserving efficiency. To minimize losses, engineers create exact seals and regulate the space between moving and stationary components. Advanced sealing methods, including brush seals and labyrinth seals, are frequently employed.
Safety and Mechanical Integrity: The design must guarantee that the turbine can run safely in all anticipated circumstances, such as emergency scenarios, shutdown, and startup. Part of designing for mechanical integrity is creating components that can tolerate high mechanical loads, thermal strains, and the effects of transient circumstances like pressure surges or steam hammers.
Flexibility and Scalability: Modern steam turbines are frequently designed with flexibility in mind to accommodate varying power outputs or industrial needs. Additionally, this modular architecture makes component replacement and maintenance easier.
Materials Used
The materials used to build steam turbines are selected based on their resistance to harsh operating conditions, which include high pressures, temperatures, and mechanical stresses. The materials chosen depend on the turbine's performance, durability, and safety.
High-Strength Alloys: Chromium-molybdenum steel and other high-strength alloys are frequently utilized for turbine rotors, casings, and other vital parts. These alloys are well-balanced in terms of strength, toughness, and resistance to thermal fatigue.
Superalloys Based on Nickel: These superalloys are commonly utilized in high-temperature areas of the turbine, like the blades and vanes in the high-pressure phases. These superalloys are perfect for applications where temperatures can reach 1000°C since they are made especially to retain their mechanical qualities at high temperatures.
Stainless Steel: Stainless steel is used for items that need to be extremely resistant to corrosion, like those that are exposed to damp steam or harsh industrial settings. Because of their ability to withstand high temperatures and their resistance to oxidation, austenitic stainless steels are preferred in particular.
Ceramic Coatings: Ceramic coatings are frequently used to improve turbine blade performance at high temperatures. By lowering the quantity of heat that is conveyed to the underlying metal, these coatings act as a thermal barrier, extending the blades' lifespan and preventing thermal deterioration.
Titanium Alloys: Because of their excellent strength-to-weight ratio and corrosion resistance, titanium alloys are occasionally utilized in low-pressure turbine blades. Their reduced density makes them useful in applications where weight reduction is crucial compared to alloys made of steel or nickel.
Creep-Resistant Materials: One major issue with steam turbines is creep, which is the propensity of materials to distort irreversibly under continuous load at high temperatures. Advanced ferritic steels and other creep-resistant materials are employed.
Manufacturing Techniques
A number of extremely specialized procedures are used in the production of steam turbines to guarantee the accurate fabrication and assembly of parts that can survive harsh operating conditions. Different techniques are employed depending on the turbine's size, complexity, and particular needs.
Casting: Many steam turbine parts, especially the rotor and casing, are made by casting methods. Melted metal is poured into a mould that is fashioned like the finished product during the casting process. When the mould is removed once the metal has solidified, a rough component that is later refined is left behind. When making complex pieces like blades, where accuracy and material integrity are essential, investment casting and sand casting are popular techniques.
Forging: Another crucial manufacturing method, forging, is used to make strong, high-integrity parts like rotors and discs. Forging aligns the grain structure of a metal workpiece by heating it and then shaping it under high pressure, improving its mechanical qualities. Generally speaking, forged parts are more robust and resistant to fatigue and creep than cast ones, which makes them perfect for high-stress turbine sections.
Machining: The majority of turbine components are machined to provide the required tolerances, surface finishes, and dimensions following casting or forging. Grinding, drilling, turning, and milling are examples of machining operations. Computer numerical control (CNC) equipment frequently ensures high precision and repeatability, particularly for parts like blades where aerodynamic qualities are crucial.
Heat Treatment: Annealing, quenching, and tempering are examples of heat treatment procedures used to improve the mechanical characteristics of turbine parts. By changing the metal's microstructure, these procedures increase the metal's strength, durability, and ability to withstand wear and thermal fatigue. Heat treatment is essential for blades that need to retain their integrity at high working temperatures.
Surface Treatments and Coatings: Turbine components frequently receive surface treatments and coatings to guard against corrosion, erosion, and high-temperature oxidation. Protective coatings are applied using methods like thermal spraying, chemical vapour deposition (CVD), and physical vapour deposition (PVD). As was previously noted, ceramic coatings are frequently used on blades to minimize heat transfer and offer thermal insulation.
Welding and combining: When assembling steam turbines, welding is an essential step, especially when combining big portions of the casing or attaching blades to the rotor. High-strength joints with few flaws are produced using sophisticated welding processes, including electron beam welding and laser welding. These methods are particularly crucial for preserving the turbine's structural soundness in high-pressure and high-temperature scenarios.
Assembly and Balancing: After every part is produced, it is meticulously assembled. One of the most important parts, the rotor, needs to be carefully balanced to guarantee smooth operation at high speeds. Balancing entails modifying the mass distribution around the rotor's axis to reduce vibrations. Usually, specialized balancing devices are used to measure and correct any imbalance.
Testing and Quality Control: Quality control is crucial in the production of steam turbines. Every component is put through a rigorous inspection and testing process to ensure it satisfies the requirements. Any internal or external flaws are found using non-destructive testing (NDT) techniques like dye penetrant examination, radiography, and ultrasonic testing. Performance testing, which involves operating the constructed turbine under controlled circumstances to confirm its output, efficiency, and operational stability, is another step in the process.
Final Assembly and Installation: The turbine is built and ready to be shipped to its installation location once all testing has been completed. To guarantee that the turbine functions properly inside its intended system—be it a power plant, industrial facility, or marine vessel—installation calls for exact alignment and calibration. Connecting the turbine to the electrical, steam supply, and other required infrastructure is part of the installation procedure.
Operation and Maintenance
Operating Conditions
Steam turbines work in harsh environments, and variables like temperature, pressure, steam quality, and load fluctuations can have a big impact on how well they work and how long they last. In order to maximize turbine functioning and guarantee dependable performance, it is imperative to comprehend these conditions.
Temperature and Pressure: High temperatures and pressures are ideal operating conditions for steam turbines. Steam enters the turbine in standard power generation applications at temperatures between 500°C and 600°C and pressures as high as 30 MPa (megapascals). Due to these severe conditions, the turbine is able to extract the most energy from the steam, but the components are subjected to significant mechanical and thermal strains.
Steam Quality: The quality of the steam entering the turbine is essential for it to operate effectively. To avoid condensation inside the turbine, which can cause blade attrition and decreased performance, the steam should ideally be dry and superheated. Saturated steam, however, may be employed in particular applications, such as nuclear power plants, necessitating careful design and management to control the risks involved.
Load Variations: Depending on the demands of the industrial process they are powering or the need for electricity, steam turbines frequently run under a variety of loads. Stable operation depends on the ability to react to load variations quickly and effectively. Turbines need to be able to ramp up or down without experiencing undue wear or damage.
Procedures for Startup and Shutdown: A steam turbine's startup and shutdown are crucial times that need to be carefully managed. To prevent thermal shocks, which can result in cracking or deformation, the turbine's components must be progressively raised to operational temperature during startup. In a similar vein, the turbine is gradually cooled during shutdown processes to avoid damage.
Control Systems: Sophisticated control systems used in contemporary steam turbines regulate several operational factors, including temperature, pressure, rotational speed, and steam flow. These mechanisms guarantee that the turbine stays within its design parameters and reacts suitably to variations in load or other operational circumstances.
Maintenance Practices
For steam turbines to remain reliable and efficient over the long term, regular maintenance is necessary. Preventive, predictive, and corrective maintenance are the three basic categories into which maintenance procedures are usually separated.
Preventive Maintenance: To stop possible problems from developing, the turbine must undergo routine inspections and servicing. This covers duties like:
Lubrication: To lessen wear and friction, lubricate bearings and other moving parts on a regular basis.
Inspection of Blades and Seals: Examining turbine blades and seals for indications of corrosion, erosion, or wear.
Cleaning: To keep turbine parts operating at their best, deposits or scales must be removed.
Calibration: Making certain that sensors and control systems are precisely calibrated to avoid operational errors.
Predictive maintenance: This method forecasts when maintenance is required before a failure happens by using condition monitoring techniques. Instead of using a set timetable, this method enables maintenance to be planned according to the turbine's actual condition. Important methods consist of:
Vibration Analysis: Tracking the turbine's vibrations to identify misalignments, imbalances, or bearing problems.
Thermography: The process of identifying hotspots or irregular temperature distributions that can point to an issue using infrared cameras.
Oil Analysis: Examining the lubricating oil for indications of chemical deterioration, wear particles, or pollution.
Corrective Maintenance: This type of maintenance is carried out to replace or repair damaged parts when a component breaks or an issue is discovered. Maintenance of this kind may include:
Blade Replacement: To restore turbine efficiency and stop additional damage, worn-out or damaged blades should be replaced.
Seal replacement or repair: Taking care of seal problems that could result in reduced efficiency or steam leaking.
Bearing Replacement: To avoid rotor unbalance and excessive vibrations, replace worn or damaged bearings.
Outage Planning: Steam turbines usually experience planned outages when performing thorough inspections, repairs, and overhauls. These outages are meticulously scheduled to reduce downtime and guarantee that the turbine is put back into service in the best possible condition. The turbine may be disassembled during an outage, and key parts such as the rotor, blades, and casing may be examined and repaired as needed.
Common Issues and Solutions
Even with their sturdy construction, steam turbines might have a number of problems when they're operating. Maintaining dependable performance requires quickly recognizing and resolving these problems.
Erosion and Blade Fouling: Fouling happens when deposits build up on the turbine blades, frequently as a result of steam impurities. However, high-velocity steam or water droplets that impinge on the blades create erosion, which progressively wears down the material. If ignored, these problems can result in decreased productivity and major harm.
Solution: While erosion-resistant coatings might prolong blade life, routine cleaning and maintenance can stop fouling. Additionally, enhancing the quality of the steam that enters the turbine can decrease the likelihood of these issues.
Vibration and Rotor Imbalance: Rotor imbalance, misalignment, bearing wear, and other mechanical issues can all contribute to excessive vibration, a typical problem in steam turbines. Accelerated component wear and, in extreme situations, catastrophic failure can result from vibration.
Solution: Vibration analysis and routine rotor balancing can help identify and address these problems before they result in serious damage. Regular bearing inspections and proper alignment during installation are also essential.
Steam Leakage: Cracks in the casing, worn seals, or inadequate sealing surfaces can all cause steam leakage. In addition to decreasing efficiency, this may harm nearby components.
Solution: Steam leaking can be reduced by routinely inspecting seals and replacing them as needed. Sometimes, a better seal and longer service life can be obtained by switching to more sophisticated sealing technologies, including brush seals.
Thermal Fatigue and Creep: Cracks develop as a result of thermal fatigue, which is brought on by repeatedly heating and cooling turbine parts. The slow deformation of materials under continuous high temperatures and stress is known as creep. Both problems have the potential to compromise the turbine's structural soundness seriously.
Solution: These dangers can be reduced by carefully controlling operation temperatures and using materials made especially to withstand thermal fatigue and creep. It's also crucial to conduct routine inspections and look for creep or tiredness.
Failures of the Control Systems: Steam turbines' control systems are essential to their safe and effective operation. Maturations in these systems may result in incorrect steam flow, pressure spikes, or even turbine trips.
Solution: Control system failures can be avoided by using redundant systems in conjunction with routine testing and calibration. Reliability can also be increased by replacing outdated systems with more contemporary digital control systems.
Applications of Steam Turbines
Power Generation
From massive thermal power plants to smaller, dispersed energy systems, steam turbines are essential to the production of electricity. The primary uses of steam turbines in power generation are described in the ensuing subsections:
Coal-Fired Power Plants:
Overview: Historically, one of the most popular uses for steam turbines has been in coal-fired power plants. Coal is burned in a boiler to create high-pressure steam in these plants, which is subsequently fed into a steam turbine to produce power.
Function of Steam Turbines: In coal-fired power plants, steam turbines are made to withstand the high pressures and temperatures involved in burning coal. An electrical generator is powered by the mechanical energy they create from the steam's thermal energy.
Environmental Considerations: Despite their efficiency, coal-fired power plants contribute significantly to greenhouse gas emissions. To increase efficiency and lower emissions, many contemporary plants use emission control systems and are switching to cleaner coal technologies, like supercritical and ultra-supercritical steam cycles.
Nuclear Power Plants:
Overview: The thermal energy produced by nuclear fission is transformed into electrical power in nuclear power plants using steam turbines. These facilities generate steam and heat water using atomic reactors.
Function of Steam Turbines: In contrast to fossil fuel facilities, the steam generated in nuclear reactors is usually produced at a lower temperature and pressure. However, because nuclear power generation is safety-critical, the turbines need to be incredibly dependable and long-lasting. Large turbines with high power outputs are frequently used in nuclear power plants in order to keep up with the reactor's constant energy production.
Special issues: Safety issues, such as the capacity to function dependably in the event of an emergency and resist the corrosive impacts of specific types of steam, are taken into account while designing steam turbines for nuclear power.
Gas-Fired Power Plants (Combined Cycle):
Overview: Gas and steam turbines are both used in combined cycle power plants to produce energy. In these plants, a steam turbine is powered by the exhaust heat from a gas turbine that produces electricity.
Function of Steam Turbines: By using the waste heat from the gas turbine, the steam turbine in a combined cycle plant increases the plant's total efficiency. This technique greatly increases the plant's thermal efficiency, frequently rising beyond 60%.
Benefits: Compared to conventional coal-fired plants, combined cycle plants are renowned for their great efficiency, flexibility, and reduced carbon emissions. Steam turbines are essential to attaining these advantages in these plants.
Geothermal Power Plants:
Overview: Geothermal energy, or the heat stored in the Earth, is used to create electricity in geothermal power plants using steam turbines.
Function of Steam Turbines: Steam is drawn from subterranean reservoirs and utilized to power turbines in geothermal plants. These turbines need to be built to withstand the possibility of corrosive gasses and minerals, as well as steam, with different temperatures and pressures.
Problems and Solutions: Scaling, corrosion, and non-condensable gas management are the primary problems in geothermal power generation. For long-term operation in these conditions, turbine designs must incorporate corrosion-resistant materials and cutting-edge sealing technology.
Solar Thermal Power Plants:
Overview: Steam turbines are used in solar thermal power plants, sometimes referred to as concentrating solar power (CSP) facilities, to produce electricity using solar radiation.
Function of Steam Turbines: In CSP plants, sunlight is focused by mirrors or lenses to heat a fluid, which is subsequently converted into steam. To generate electricity, steam powers a turbine, which transforms thermal energy into mechanical energy.
Innovations: Some CSP facilities incorporate thermal storage devices, which enable them to produce power even in the absence of sunlight. These plants' steam turbines need to be able to work well with the thermal storage systems and adjust to different steam inputs.
Industrial Applications
Steam turbines provide mechanical power for various applications in industrial operations and power generation.
Petrochemical Industry:
Overview: Steam turbines are crucial to the petrochemical sector. They power compressors, pumps, and other equipment required in the manufacturing of chemicals and petroleum products.
Function of Steam Turbines: under this sector, steam turbines are frequently made to run continuously, efficiently, and dependably under challenging circumstances, such as hot temps and corrosive surroundings.
Benefits: Steam turbines in petrochemical facilities contribute to increased overall energy efficiency by recovering waste heat and turning it into usable mechanical or electrical energy.
Pulp and Paper Industry:
Overview: Steam turbines are used in the pulp and paper industry to generate electricity and power mechanical processes like pulping, drying, and papermaking.
Function of Steam Turbines: In this sector, steam turbines are frequently used in cogeneration systems, which generate steam for manufacturing and electricity simultaneously. This combined heat and power (CHP) method improves energy efficiency.
Problems: The primary issues are managing varying loads and guaranteeing dependable performance in settings with high moisture content and potentially corrosive substances.
Steel Manufacturing:
Overview: Steam turbines power blowers, compressors, and rolling mills in the steel industry. The technique is more energy-efficient because the steam used frequently originates from waste heat recovery systems.
Function of Steam Turbines: Steam turbines help lower steel mills' total energy usage by using waste heat to produce electricity for various operations.
Benefits: Integrating steam turbines into steel production processes helps meet environmental laws while also saving energy expenses. Reducing pollutants also reduces energy expenses.
Sugar Industry:
Overview: Steam turbines are widely used in the sugar business to produce ethanol and sugar. They are a component of cogeneration systems that run on bagasse, the fibrous waste that remains after sugar juice is extracted.
Steam turbines in this sector produce electricity and supply mechanical power for crushing and refining operations. Utilizing biomass, such as bagasse, lessens reliance on fossil fuels and makes the process more sustainable.
Sustainability: The use of steam turbines in sugar manufacturing demonstrates how renewable energy sources can be used in industrial settings.
Marine Propulsion
Historically, steam turbines have been used for maritime propulsion, especially in big commercial ships and military boats. They are perfect for this demanding application because of their power production, dependability, and efficiency.
Naval Vessels:
Overview: Steam turbines have historically been a key component of naval propulsion, particularly in large ships like submarines, destroyers, and aircraft carriers.
Function of Steam Turbines: Naval turbines are built to be dependable, efficient, and capable of producing large amounts of power. They are required to operate under extreme operating circumstances, including abrupt speed changes and extended high-speed operation.
Developments: Modern naval steam turbines frequently use cutting-edge materials and cooling technology to survive the severe sea environment and run silently—two qualities essential for military operations involving stealth.
Commercial Shipping:
Overview: Large ships like tankers and bulk carriers in commercial shipping employ steam turbines. Steam turbines are still utilized in some applications, especially those requiring high power and long-range operation, even though diesel engines are now more prevalent.
Benefits: Compared to alternative propulsion systems, steam turbines provide smooth operation, less vibration, and less maintenance, which makes them appropriate for large ships.
Trends: As more fuel-efficient diesel engines have become available, steam turbines have been less common in commercial ships. Nonetheless, they continue to be utilized in some situations where their advantages surpass those of substitute technology.
Renewable Energy Integration
Additionally, steam turbines are being used in renewable energy systems, which helps to produce sustainable and clean energy.
Biomass Power Plants:
Overview: Biomass power plants create energy by using organic materials like garbage, wood, and agricultural residues to produce steam, which powers turbines.
Function of Steam Turbines: Steam turbines in biomass plants are required to manage steam produced from a range of biomass sources, which can differ in terms of consistency and quality. The flexible and effective design of the turbines maximizes the energy that may be obtained from biomass.
Environmental Benefits: Because the CO2 absorbed during biomass growth balances the CO2 released during combustion, biomass power generation is regarded as carbon-neutral. Thanks in large part to steam turbines, this is a practical and sustainable energy source.
Concentrated Solar Power (CSP):
Overview: Solar energy is converted into electrical power in CSP plants using steam turbines. The plants focus sunlight onto a receiver using mirrors or lenses, which then heats a fluid to create steam.
Function of Steam Turbines: CSP plants' turbines need to be built to run effectively on steam produced by varying solar input and to interface with thermal storage devices, which enable power output even in the absence of sunlight.
Innovation and Prospects for the Future: Steam turbines are anticipated to become more significant in supplying dispatchable, renewable electricity as CSP technology develops. This will aid in stabilizing grids that heavily rely on intermittent renewable sources like solar PV and wind.
Efficiency and Performance Optimization
Factors Affecting Efficiency
An essential component of a steam turbine's operation is its efficiency, which affects the energy conversion process as a whole as well as the financial sustainability of power plants and industrial uses. A steam turbine's efficiency can be affected by a number of factors:
Steam Conditions:
Temperature and Pressure: The potential for energy extraction increases with the temperature and pressure of the steam at the turbine inlet. Because superheated steam has a higher energy content, the turbine can do more work, which boosts efficiency. Nonetheless, the design and materials used must be able to resist these harsh circumstances.
Steam Quality: Turbine performance is influenced by the quality of the steam, especially its dryness fraction. Because wet steam contains water droplets, it can erode turbine blades and decrease efficiency. These losses can be reduced by superheating the steam or by maintaining a high dryness fraction.
Design and Aerodynamics:
Blade Design: The effectiveness of turbine blades is greatly influenced by their shape, angle, and surface finish. More efficient energy conversion from steam to mechanical work is made possible by aerodynamically designed blades, which minimize losses from turbulence and friction.
Efficiency of the Stages: Steam turbines are frequently separated into several stages, each intended to draw energy from steam at increasingly lower pressures. The effectiveness of each stage influences total turbine efficiency. Optimizing efficiency requires proper staging with precisely measured blade profiles and angles.
Mechanical Losses:
Friction and Wear: Mechanical losses caused by friction in bearings, seals, and other moving parts can decrease a turbine's total efficiency. Cutting-edge materials, adequate lubrication, and routine maintenance can reduce these losses.
Vibration and Imbalance: Excessive vibrations or rotor imbalances can result in mechanical inefficiencies, as energy is wasted as undesired movements occur. It is essential to ensure that the turbine is balanced correctly and that efficient dampening systems manage vibrations.
Thermodynamic Losses:
Heat Losses: Heat losses happen when steam or other elements transfer heat to the surroundings. Reducing the temperature gradient inside the turbine and properly insulating the pipes and turbine housing can help lower these losses.
Entropy Generation: Inefficiencies in the turbine stages' expansion process may result in higher entropy, which would lower the amount of work produced. Optimizing the expansion process and avoiding irreversible losses within the turbine are two ways to reduce these losses.
Optimization Techniques
Steam turbine efficiency can be increased by combining technology advancements, operational tactics, and design improvement. To improve turbine performance, the following methods are frequently employed:
Advanced Blade Design:
Computational Fluid Dynamics (CFD): CFD is frequently utilized in turbine blade design and optimization. By modelling the steam flow through the turbine, engineers can pinpoint regions of loss and modify blade designs and angles to increase efficiency. CFD eliminates the requirement for physical prototypes by enabling the testing of several design iterations in a virtual setting.
3D Blade Profiling: Advanced manufacturing techniques like 3D printing and precision machining can produce complex blade profiles suited to particular operating circumstances. Blades that have undergone 3D profiling can achieve better aerodynamic performance and lower losses.
Steam Temperature and Pressure Control:
Superheating and Reheating: Efficiency can be greatly increased by either reheating steam in between turbine stages or by raising the temperature of steam prior to it entering the turbine (superheating). For example, reheating lowers the moisture content in the turbine's later stages, enabling more energy extraction.
Pressure Optimization: Efficiency can be increased by running the turbine at the ideal steam pressure for each stage. The steam pressure throughout the turbine must be meticulously controlled to ensure that every stage runs at its most efficient location on the pressure-enthalpy curve.
Energy Recovery Systems:
Regenerative Feedwater Heating: This method uses steam obtained from the turbine's intermediate stages to warm the feedwater before it enters the boiler. This increases the Rankine cycle's total efficiency because less fuel is required to reach the appropriate steam temperature.
Condensate Recovery: Reducing the energy needed to heat and pressurize water for later cycles can be achieved by effectively recovering and reusing condensate (water) from turbine exhaust. Additionally, this reduces the need for extra water treatment, which raises total efficiency.
Load Optimization:
Variable Load Operation: Contemporary steam turbines are built to function well under a variety of loads, not just when they are operating at maximum capacity. Power plants can increase overall efficiency by optimizing turbine performance under partial loads, particularly in applications where demand varies throughout the day.
Load matching is the process of modifying the turbine's operation to correspond with the particular energy demand at any given moment. To meet the load's needs in real-time, this may entail regulating the turbine's output, changing the number of active turbine stages, or altering the steam flow rate.
Monitoring and Control Systems:
Real-Time Performance Monitoring: Thanks to sophisticated sensors and control systems, temperature, pressure, vibration, and efficiency parameters may all be tracked in real-time. By regularly monitoring these parameters, operators can optimize performance and avert problems before they result in breakdowns or inefficiencies.
Predictive maintenance: Using data analytics and machine learning, predictive maintenance systems can predict possible problems based on past performance data. This allows for preventative maintenance, which lowers downtime and raises turbine efficiency overall.
Monitoring and Performance Analysis
Continuous performance data analysis and monitoring are necessary to maintain steam turbines' maximum efficiency. The methods listed below are frequently employed to evaluate and improve turbine efficiency:
Key Performance Indicators (KPIs):
Heat Rate: The heat rate indicates how much energy the turbine uses to produce electricity. It is usually stated as the quantity of fuel energy needed per electrical output unit (e.g., BTU/kWh). Monitoring the heat rate can help identify fuel and turbine performance inefficiencies.
Thermal Efficiency: The ratio of usable work production to total heat input is known as thermal efficiency. It is a crucial sign of how well thermal energy is transformed into mechanical energy by the turbine. Higher thermal efficiency indicates better performance.
Capacity Factor: This is the ratio of the turbine's actual output over time to its maximum output potential. It shows the efficiency of the turbine's use in relation to its maximum capacity.
Performance Testing:
Acceptance Testing: To ensure a turbine meets the required performance standards, acceptance testing is carried out either upon initial installation or following a significant overhaul. Under controlled circumstances, these tests usually examine variables, including output power, efficiency, and steam consumption.
Routine Testing: Performance tests are carried out regularly to monitor the turbine's continuous efficiency. Regular testing allows us to identify slow performance drops and take prompt action to boost productivity.
Data Analytics and Optimization:
Data Logging and Trend Analysis: Constant data logging allows for the gathering of enormous volumes of performance data, which can then be examined to spot patterns, find irregularities, and determine how operational adjustments affect productivity.
Digital Twins: A steam turbine's virtual model that replicates its real-world equivalent in real-time is called a digital twin. By contrasting the performance of the digital twin with actual operational data, operators can find inefficiencies and test possible enhancements without endangering the real turbine.
Diagnostic Tools:
Vibration Monitoring: A vital diagnostic technique for identifying mechanical problems such as rotor imbalance, misalignment, or bearing wear is vibration analysis. Operators can prolong the turbine's life and avoid efficiency losses by spotting and fixing these problems early.
Thermal Imaging: Thermal imaging evaluates the temperature distribution among the turbine's components and identifies hotspots. This makes it easier to spot places where heat loss is occurring and where cooling or insulation may be required.
Environmental Impact and Sustainability
Environmental Concerns
Despite being essential to industrial operations and electricity generation, steam turbines raise a number of environmental issues. The energy sources utilized to generate steam and the byproducts of turbine operation are the main causes of these problems.
Greenhouse Gas Emissions:
Fossil Fuel Combustion: Carbon dioxide (CO2) and other greenhouse gases are largely released by steam turbines found in coal, oil, and natural gas-fired power plants. One of the main causes of climate change and global warming is CO2, which is released when fossil fuels are burned.
Mitigation Strategies: Some ways to lower greenhouse gas emissions are increasing the efficiency of steam turbines, switching to cleaner fuels, and incorporating carbon capture and storage (CCS) technology. Because less fuel is needed to generate the same quantity of power, higher efficiency lowers emissions per unit of energy produced.
Air Pollutants:
Sulfur Dioxide (SO2) and Nitrogen Oxides (NOx): When fossil fuels are used in power plants, toxic air pollutants like SO2 and NOx are released. These pollutants can cause acid rain and respiratory issues in people. Because coal-fired power stations have a higher sulfur concentration in their fuel, these pollutants are more common there.
Control Technologies: To lower SO2 and NOx emissions from power plants, technologies like selective catalytic reduction (SCR) and flue gas desulfurization (FGD) are employed. Low-NOx burners and other methods of combustion optimization further reduce the production of these pollutants at the source.
Water Usage and Thermal Pollution:
Requirements for Cooling Water: Steam turbines, especially in large power plants, need a lot of water to cool. Removing water from natural sources may impact local ecosystems, particularly if it is not handled sustainably. Additionally, thermal pollution, which harms aquatic life, can result from the release of heated water back into the environment.
Mitigation Strategies: Power plants can use closed-loop cooling systems that minimize thermal discharge and water withdrawal to lessen these effects. Additionally, especially in areas with limited water supplies, dry cooling systems—which use air rather than water—are being used more and more.
Solid Waste and Byproducts:
Coal Ash and Slag: Solid byproducts like ash and slag, which can include heavy metals and other hazardous materials, are produced when coal is burned in power plants. Careful management of these leftovers is necessary to avoid contaminating the soil and water.
Ash can be safely disposed of in lined landfills as part of modern waste management techniques, and it can also be usefully recycled into building materials like concrete and cement. Turning waste into useful products can reduce the negative effects of coal ash on the environment.
Sustainability Initiatives
Due to environmental concerns, the steam turbine sector is increasingly embracing sustainability measures to lessen its environmental impact and aid in the shift to a low-carbon economy.
Integration with Renewable Energy:
Biomass and Waste-to-Energy: Steam turbines are being combined with waste-to-energy facilities and biomass, two renewable energy sources. These systems generate steam from biological waste materials, which steam turbines subsequently use to generate power. Because the CO2 absorbed during biomass growth balances the CO2 released during combustion, biomass is regarded as carbon-neutral.
Geothermal and Solar Thermal: Steam turbines are another method used by geothermal and concentrated solar power (CSP) facilities to produce electricity. These renewable energy sources are appealing choices for environmentally friendly power generation since they emit few or no greenhouse gases. In these environments, the usage of steam turbines promotes the wider uptake of renewable energy technology.
Efficiency Improvements:
Supercritical and Ultra-Supercritical Steam Cycles: Supercritical and ultra-supercritical steam cycles, which function at higher temperatures and pressures than traditional steam cycles, are the result of developments in turbine technology. Because these cycles are more efficient, less fuel is required to generate the same quantity of energy, which lowers emissions.
Cogeneration and Combined Heat and Power (CHP): Cogeneration, also known as CHP, systems employ the same energy source to generate both useful heat and power. CHP systems greatly increase total energy efficiency by absorbing and using steam turbine waste heat, which lowers emissions and fuel consumption.
Carbon Capture and Storage (CCS):
Carbon capture and storage, or CCS, is a technology intended to absorb CO2 emissions from factories and power plants and keep them out of the environment. After being captured, the CO2 is moved and kept underground in geological formations. When combined with steam turbines, CCS can significantly lower the carbon footprint of fossil fuel-based power generation.
Opportunities and Challenges: Although CCS can slow global warming, it has drawbacks, including high prices, energy demands, and the requirement for appropriate storage locations. Ongoing research and development initiatives, however, aim to overcome these obstacles and make CCS a practical choice for significant emission reductions.
Material and Resource Efficiency:
Recycling and Waste Reduction: The steam turbine sector is implementing strategies to reduce waste and boost resource effectiveness. This includes reducing material waste through precision manufacturing techniques and reusing metals and other materials used in turbine production.
Life Cycle Assessment (LCA): This method is used to analyze how a product affects the environment at every stage of its life cycle, from the
extraction of raw materials to disposal. Manufacturers can find areas where environmental impacts can be minimized through life cycle assessments (LCAs), which will result in more sustainable turbine production and operation.
Regulatory Framework
Steam turbines, especially those used in power generation, must adhere to several environmental laws to reduce their environmental impact. Although these laws differ by area, they usually centre on waste management, water use, and emissions reduction.
Emissions Regulations:
U.S. Clean Air Act: The Clean Air Act (CAA) governs air pollutants from industrial sources, including steam turbines and power plants in the United States. The CAA requires the adoption of the best available control technologies (BACT) to decrease emissions and sets limitations for pollutants like SO2, NOx, and particulate matter.
EU Emissions Trading System (EU ETS): This cap-and-trade system places a cap on the overall quantity of greenhouse gases that specific industries, such as electricity generating, are permitted to emit. In the EU, steam turbine operators are required to adhere to emission allowances or buy extra allowances if they surpass them.
Water Usage and Discharge Regulations:
U.S. Clean Water Act: The Clean Water Act (CWA) establishes water quality standards and controls the release of pollutants into American waters. To prevent their operations from endangering aquatic ecosystems, power plants that use steam turbines are required to get permits for the withdrawal and release of water.
EU Water Framework Directive: The Water Framework Directive regulates water use and thermal discharges from power plants and provides a framework for safeguarding water resources throughout the EU. Adherence to these rules is necessary for steam turbines to operate sustainably.
Waste Management and Disposal:
RCRA, or the Resource Conservation and Recovery Act, regulates the handling of hazardous and non-hazardous waste in the United States, including coal ash from power plants. The act promotes the recycling and reuse of industrial waste and mandates safe disposal procedures.
EU Waste Framework Directive: The EU Waste Framework Directive encourages recycling and the decrease of waste generation by establishing rules for waste management among its member states. Operators of steam turbines are required to abide by these rules in order to reduce their environmental impact.
International Standards and Guidelines:
Environmental Management Systems: The ISO 14001 standard gives businesses a framework for methodically handling their environmental obligations. By adhering to ISO 14001, steam turbine operators can increase sustainability and lessen their environmental impact.
World Bank Environmental and Social Standards (ESS): The World Bank's Environmental and Social Standards (ESS) provide Guidelines for controlling environmental and social risks in World Bank-financed projects. These requirements are frequently applied when building power plants and other large-scale steam turbine projects.
Future Trends and Innovations
Technological Advances
The need for increased efficiency, dependability, and environmental performance is driving the ongoing evolution of the steam turbine sector. A number of technological developments are influencing how steam turbines will develop in the future:
Advanced Materials:
Superalloys: The creation of sophisticated nickel-based superalloys is increasing the efficiency of steam turbines by allowing them to run at higher pressures and temperatures. These materials are perfect for usage in the most demanding parts of the turbine since they are made to withstand creep, corrosion, and thermal fatigue.
Ceramic Matrix Composites (CMCs): CMCs are attracting interest due to their potential to take the place of conventional metal alloys in high. Because of these materials' superior oxidation resistance, low density, and thermal stability, turbines can run at even greater temperatures without losing structural integrity.
Additive Manufacturing: Often referred to as 3D printing, additive manufacturing is transforming the way turbine parts are made. This technology allows for the creation of complex, optimized geometries that are hard or impossible to accomplish using conventional manufacturing techniques. Additionally, additive manufacturing speeds up production and minimizes material waste.
Advanced Blade Design:
3D-Aerodynamic Blades: Steam turbine performance and efficiency are being enhanced by advancements in blade design, especially the application of 3D aerodynamic modelling. By maximizing steam flow, these blades minimize losses from friction and turbulence. Engineers can optimize blade designs with the use of computational fluid dynamics (CFD) simulations.
Shrouded and Shroudeless Blades: To increase efficiency even more, shrouded blades—which have a cover on the tips to prevent leaks—are being refined. Meanwhile, developments in shroudless blade designs are being investigated in an effort to preserve aerodynamic performance while lowering weight and mechanical complexity.
Digitalization and Smart Turbines:
Digital Twins: A virtual replica of a steam turbine that operates in tandem with the real machine is known as a "digital twin," and it is quickly emerging as a crucial instrument in the industry. With digital twins, operators can forecast maintenance requirements, improve operations, and track turbine performance in real-time. By modelling various situations, digital twins can assist in anticipating possible problems and recommending the best course of action for maintenance or operational changes.
Artificial Intelligence (AI) and Machine Learning: These two fields are being utilized more and more to improve turbine control systems. With the help of these technologies, operating parameters like temperature, pressure, and steam flow can be more precisely controlled, maximizing turbine efficiency under various load scenarios. In addition to predicting equipment failures, AI-driven analytics can prolong the life of turbine components and minimize downtime.
Modular and Scalable Designs:
Modularity: The development of modular steam turbines is a movement aimed at increasing flexibility and cutting costs. Modular turbines are appropriate for both large-scale power plants and smaller, decentralized energy systems since they are simple to scale up or down according to power generation needs. Additionally, modularity reduces downtime by making maintenance and component replacement simpler.
Scalability for Microgrids: Distributed energy systems and microgrids are using steam turbines. These scalable turbines are intended to supply dependable electricity in isolated areas or as a component of a hybrid energy system that combines conventional power generation with renewable energy sources.
Integration with Smart Grids
Steam turbines are being incorporated into smart grid systems, which, as the energy landscape changes, provide more flexibility, dependability, and efficiency in power generation and delivery.
Role of Steam Turbines in Smart Grids:
Load Balancing: Steam turbines are crucial to smart grid load balancing, especially during high demand. They can be turned up or down to meet demand, keeping the system stable and preventing blackouts. Because they can react swiftly to demand fluctuations, steam turbines are an important part of smart grids.
Integration with Renewable Energy: Renewable energy sources like wind and solar are being progressively integrated into smart grids. When renewable energy sources are sporadic, steam turbines—especially those found in combined heat and power (CHP) plants—can deliver backup power, guaranteeing a steady and dependable energy supply. Steam turbines can operate more efficiently by integrating with smart grid technologies, which use real-time grid data.
Advanced Control Systems:
Real-Time Monitoring and Control: To make steam turbines run more effectively in a smart grid, sophisticated control systems are being created. In order to maximize performance, these systems modify operating parameters like steam pressure and temperature based on real-time data. Additionally, real-time monitoring lowers maintenance expenses and downtime by identifying possible problems before they become failures.
Grid Synchronization: To enable smooth integration with smart grids, steam turbines are being outfitted with cutting-edge synchronization technologies. By ensuring that the turbines can synchronize their output with the grid's frequency and voltage, these technologies preserve the power's dependability and quality.
Demand Response and Energy Storage:
Demand Response Programs: These programs involve steam turbines, in which electricity generation is modified in response to current demand. By lowering their output during low demand or increasing it during peak times, steam turbines can balance the grid and lessen the need for additional peaking power plants.
Integration with Energy Storage: To increase their adaptability and efficiency, steam turbines are being combined with energy storage devices like thermal storage and batteries. Energy storage increases grid stability and efficiency by enabling turbines to store excess energy generated during times of low demand and release it when needed.
Research and Development
The goal of ongoing research and development (R&D) is to advance steam turbine technology, fulfil changing energy market demands, and tackle environmental issues.
High-Efficiency Steam Cycles:
Supercritical and Ultra-Supercritical Cycles: Developed at greater temperatures and pressures than traditional cycles, supercritical and ultra-supercritical steam cycles are being propelled by research and development. By providing greater thermal efficiencies, these sophisticated cycles lower emissions and fuel consumption. To survive the harsh circumstances of these cycles, researchers are investigating novel materials and designs.
Thermodynamic Cycle Innovations: Novel thermodynamic cycles, such as the Organic Rankine Cycle (ORC) and the Kalina cycle, are being investigated for their capacity to increase efficiency in particular applications. These cycles employ various working fluids or configurations to maximize energy conversion, especially in low-temperature or waste heat recovery applications.
Low-Carbon and Carbon-Neutral Technologies:
Hydrogen-Fueled Steam Turbines: Research is being done to create steam turbines that run on hydrogen, a fuel that doesn't include carbon and can be generated using renewable energy. When combined with renewable energy sources, hydrogen-fueled turbines have the potential to create dependable, low-carbon electricity.
Carbon Capture Integration: One of the main areas of research focused on lowering CO2 emissions from fossil fuel-based power generation is the integration of carbon capture and storage (CCS) technology with steam turbines. The goal of ongoing research and development is to increase CCS's effectiveness and affordability so that it may be implemented on a big scale.
Enhanced Durability and Reliability:
Advanced Coatings and Surface Treatments: Research and development is concentrated on creating advanced coatings and surface treatments that can shield turbine parts from erosion, corrosion, and high-temperature oxidation, thereby extending their lifespan. These coatings are crucial for enhancing the robustness and dependability of turbines that operate in challenging environments.
AI and Predictive Maintenance: Research into AI—and machine learning-driven predictive maintenance solutions are contributing to increased steam turbine reliability. These technologies make it possible to estimate maintenance requirements more precisely, minimizing unplanned downtime and prolonging the life of turbine components by examining past performance data and spotting trends that precede failures.
Challenges and Opportunities
The steam turbine industry's future will be shaped by the possibilities and problems it faces as it develops.
Challenges:
Environmental rules: The steam turbine sector faces challenges from increasingly strict environmental regulations, especially those pertaining to water use and greenhouse gas emissions. Continuous innovation in turbine design, materials, and operating procedures is necessary to meet these standards.
Competition from Alternative Technologies: The steam turbine sector faces competition from emerging alternative power production technologies like wind, solar, and energy storage. Policies aiming at lowering carbon emissions frequently favour these technologies, which are becoming more cost-competitive.
Ageing Infrastructure: Many steam turbines, especially those in older power facilities, are nearing the end of their operating lives. Upgrading or replacing ancient turbines with more contemporary, efficient designs is quite difficult, especially in terms of downtime and expense.
Opportunities:
Decarbonization Initiatives: The steam turbine sector can create low-carbon and carbon-neutral technology to meet global decarbonization goals. Steam turbines can be combined with renewable energy, hydrogen, and CCS.
Energy Transition: As the energy industry changes to more sustainable sources, steam turbines can help hybrid systems generate power from renewable and traditional sources. Reliable, uninterrupted power from hybrid systems reduces carbon emissions.
Emerging Markets: Asia and Africa provide steam turbine sector growth potential. Industrialization and energy infrastructure expansion in these regions will raise demand for reliable and efficient power production technologies like steam turbines.
Case Studies and Industry Examples
Notable Projects
Real-world steam turbine applications demonstrate its versatility and efficiency across industries. Case studies show substantial installations and steam turbine effects in various settings:
The Taichung Power Plant, Taiwan:
Overview: Taiwan's Taichung Power Plant is one of the world's largest coal-fired power plants. Its 5,500 MW installed capacity helps meet Taiwan's population and industry's energy needs.
Steam Turbines: The facility converts coal combustion heat into electricity using massive steam turbines. High-efficiency supercritical steam turbines enhance energy extraction.
Environmental Impact: Taichung, a coal-fired plant, uses flue gas desulfurization and selective catalytic reduction to reduce its environmental impact. The facility also sets efficiency standards for large-scale fossil fuel power generation.
The Olkaria Geothermal Plant, Kenya:
Overview: Kenya's Great Rift Valley hosts Africa's largest geothermal power facility, Olkaria. It boosts Kenya's renewable energy mix with about 800 MW of capacity.
Steam Turbines: The facility uses steam turbines built to handle geothermal steam's corrosive gasses and minerals. Geothermal turbines generate reliable, low-carbon electricity.
Sustainability: The Olkaria Geothermal Plant shows that geothermal energy may provide baseload power in geothermal zones. The plant's growth shows geothermal projects' scalability and steam turbines' importance in renewable energy.
The Ivanpah Solar Electric Generating System, United States:
Overview: In California's Mojave Desert, Ivanpah is one of the world's largest CSP plants. Mirrors focus sunlight on boilers to generate steam to drive turbines at 392 MW.
Steam Turbines: Ivanpah's steam turbines function with CSP plants' variable steam input. These important components transform solar energy into electricity by starting and stopping swiftly in response to solar conditions.
Innovation: Ivanpah shows how steam turbines can work in renewable energy systems. The project combines modern steam turbine technology with CSP technology to generate utility-scale renewable energy.
Industry Leaders
Many firms and institutes have helped design and install steam turbines. These industry giants have pioneered technology and set efficiency and reliability standards.
Siemens Energy:
Overview: Siemens Energy is a global leader in steam turbine design and manufacturing for power generating, industrial, and marine propulsion. Innovation and efficiency are corporate hallmarks.
Key Contributions: Siemens pioneered high-efficiency steam turbines for supercritical and ultra-supercritical applications. Power plants worldwide use their turbines for fossil fuel and renewable energy projects. Siemens leads digitalization with advanced monitoring and control technologies that improve turbine performance and reliability.
General Electric (GE):
Overview: Another significant steam turbine manufacturer, General Electric, has a long history of invention and engineering excellence. GE steam turbines are used in power generation, industrial operations, and marine propulsion.
Key Contributions: GE's high-performance blades, innovative materials, and integrated control systems have improved turbine efficiency. As a pioneer in digital twins and predictive maintenance, the business has helped operators enhance turbine performance and decrease operational costs.
Mitsubishi Power:
Overview: Mitsubishi Power, a Mitsubishi Heavy Industries company, is an Asian leader in steam turbine manufacturing. The company manufactures turbines for coal, nuclear, gas, and renewable energy facilities.
Key Contributions: Mitsubishi Power designs efficient, reliable steam turbines. The company has advanced ultra-supercritical turbine development and large-scale geothermal and biomass projects. Mitsubishi Power also researches hydrogen-powered turbines and carbon capture integration.
Lessons Learned
Steam turbine deployment in many sectors reveals their problems and best practices. Lessons from these efforts include:
The Importance of Customization:
Project-Specific Design: Successful steam turbine projects teach the importance of customization. Each project has unique requirements due to fuel, operational circumstances, and environmental rules. These conditions must be considered when designing the steam turbine for the best performance and reliability.
Adaptation to Local Conditions: The Olkaria Geothermal Plant needed to adjust the turbine design to geothermal steam's high moisture content and corrosive gasses for long-term performance. Understanding local circumstances and implementing them into turbine design is crucial.
Efficiency as a Key Driver:
Efficiency: To reduce fuel consumption and pollutants, steam turbine development has prioritized efficiency. The Taichung Power Plant shows how supercritical and ultra-supercritical steam conditions can boost efficiency, lowering operational costs and environmental effects.
Blade Design Innovation: 3D-aerodynamic blades and innovative materials have improved turbine efficiency. Industry giants like Siemens and GE demonstrate that turbine component innovation is essential to market competitiveness.
The Role of Digitalization:
Adopting Digital Technologies: Digital twins, AI, and real-time monitoring systems are best practices in the steam turbine industry. These technologies help operators maximize performance, estimate maintenance needs, and reduce downtime, improving efficiency and reliability.
Data-driven decision making: Monitoring turbine performance and predicting faults with data analytics is becoming more critical. Industry leaders have shown that data-driven decision-making improves steam turbine efficiency and lifespan.
Sustainability and Environmental Compliance:
Sustainability Initiatives: Due to sustainability concerns, steam turbine projects now use biomass, geothermal, and solar thermal energy. Projects like Ivanpah demonstrate that steam turbines may help shift to renewable energy if integrated with the right technologies.
Regulatory Compliance: Steam turbine projects must follow environmental rules. Taichung Power Plant's successful deployment of emission control technology shows the necessity of following regulatory criteria to reduce environmental impact and assure project sustainability.
Conclusion
Summary of Key Points
For more than a century, steam turbines have been a mainstay of industrial and power generation applications, exhibiting exceptional versatility and efficiency in a range of contexts. This thorough examination of steam turbines has addressed their development over time, basic concepts, design and manufacturing procedures, and the diverse range of applications they find use in.
Basics: Steam turbines work by transforming steam's thermal energy into mechanical energy, which can be utilized to power machinery or produce electricity. Steam temperature, blade design, and the thermodynamic cycles used—the most popular being the Rankine cycle—all affect the efficiency of this operation.
Design and Manufacturing: Thermodynamics, materials science, and mechanical engineering must all be carefully considered during the intricate process of designing steam turbines. Turbine efficiency and dependability are increasing due to developments in blade design and digitization, as well as advancements in materials like superalloys and ceramic matrix composites. Casting, forging, machining, and heat treatment are all steps in the production process that guarantee turbines can survive harsh operating environments.
Operation and Maintenance: To guarantee their longevity and optimal performance, steam turbines need to be operated carefully and receive routine maintenance. Problems like steam leakage, rotor imbalance, and blade attrition can be avoided with the use of sophisticated diagnostic equipment and maintenance techniques, including predictive and preventive maintenance. Proper operation, which includes controlling the quality of the steam and following starting and shutdown protocols, is also necessary to optimize efficiency and reduce wear.
Applications: Steam turbines are employed in many different processes in the steel, petrochemical, and pulp and paper industries, as well as in power generation in coal, nuclear, and geothermal plants. Additionally, they are essential for naval propulsion and are being used more and more in renewable energy sources like biomass and concentrated solar power.
Efficiency and Optimization: Steam turbines' performance is largely determined by their efficiency, which is continuously improved by developments in energy recovery systems, steam conditions, and blade design. Digital twins, artificial intelligence, and real-time monitoring systems are improving the ability to maximize turbine performance, minimize downtime, and prolong the lifespan of turbine components.
Sustainability and Environmental Impact: Steam turbines' effects on the environment, especially those driven by fossil fuels, are a major worry. However, these effects are being lessened, and the shift to a low-carbon future is being supported by sustainability measures like the use of carbon capture technology, the development of supercritical and ultra-supercritical steam cycles, and the integration of renewable energy sources.
Future Trends and Innovations: The steam turbine sector is expected to experience further innovation in the years to come, driven by developments in digitalization, materials science, and smart grid integration. Research into low-carbon and carbon-neutral technology, such as increased carbon capture systems and turbines powered by hydrogen, will greatly aid the industry's development. The sector faces both potential and challenges due to ageing infrastructure, competition from alternative technologies, and environmental laws.
The Future of Steam Turbines
Steam turbines will continue to be essential to industrial operations and power generation as the world's energy landscape changes. Thanks to their capacity to adjust to evolving technology, integrate with renewable energy sources, and increase efficiency, they will remain relevant in the ensuing decades.
The drive for decarbonization and the demand for more environmentally friendly energy sources will fuel further advancements in steam turbine technology. Meeting the increasing need for clean, dependable, and efficient power will require the development of ultra-efficient steam cycles, the incorporation of digital technologies, and the investigation of novel materials and designs.
Furthermore, steam turbines provide substantial growth potential in emerging economies and in hybrid energy systems that blend conventional power generation with renewable resources. The need for steam turbines that can provide high efficiency, dependability, and sustainability will grow as these areas continue to industrialize and develop their energy infrastructure.
In summary, steam turbines have a long history of invention and adaptability. As they develop further in response to the opportunities and challenges of the twenty-first century, their future is bright. Steam turbines will continue to be a vital component of the world's energy generation for many years to come thanks to the continuous efforts to increase efficiency, lessen their negative effects on the environment, and integrate with cutting-edge energy systems.
Introduction to Power Generation with Steam Turbines
For more than a century, steam turbines have been the mainstay of power generation. Invented by Sir Charles Parsons in 1884, steam turbines swiftly rose to prominence as the primary method of transforming thermal energy into mechanical energy and then electrical energy. Due to their efficiency and adaptability, they are the foundation of electricity generation globally.
Steam turbines are employed in many different contexts in contemporary power generation, ranging from massive fossil fuel facilities to renewable energy installations. Their working idea is to drive a rotor coupled to a generator to transform the energy from high-pressure steam into mechanical energy. Because of their adaptability, steam turbines can be used in a variety of energy systems, such as solar thermal, geothermal, coal, nuclear, and natural gas power plants.
The capacity of steam turbines to effectively generate substantial amounts of electricity is what makes them significant. As technology has advanced, steam turbines can now function at higher pressures and temperatures, which boosts efficiency and lowers fuel usage. Steam turbines are an essential part of the shift to more sustainable energy systems because of these advancements, which have also resulted in a decrease in greenhouse gas emissions per unit of electricity produced.
Types of Power Plants Using Steam Turbines
Coal-Fired Power Plants
One of the most popular uses for steam turbines is in coal-fired power plants. In these plants, coal is burned in a boiler to create high-pressure steam, which is subsequently fed into a steam turbine to produce power. Despite its negative environmental effects, including CO2 emissions and air pollution, coal is still a major source of energy, especially in developing nations.
As steam turbine technology has advanced over time, coal-fired power plants have become more efficient. Higher thermal efficiency is made possible by supercritical and ultra-supercritical steam conditions, in which steam is produced at pressures and temperatures above the critical point. This lessens the total impact on the environment because more electricity can be created from the same amount of coal.
Emission control methods like selective catalytic reduction (SCR) and flue gas desulfurization (FGD) lower pollutants like SO2 and NOx emissions. Furthermore, although they are still in the early phases of adoption, carbon capture and storage (CCS) technologies are being developed to absorb CO2 emissions from coal plants.
Nuclear Power Plants
Steam turbines are essential for turning nuclear fission heat into electrical power in nuclear power plants. Water is heated in nuclear reactors to create steam, which powers a steam turbine that is connected to a generator. Because nuclear energy is safety-critical, the steam turbines used in nuclear power facilities are usually enormous and require a high degree of reliability.
One of the main issues in nuclear power generation is managing the steam conditions, which are different from those in fossil fuel plants. Certain turbine designs must function well in nuclear reactors because the steam they produce is frequently at lower temperatures and pressures. The turbines also need to be able to survive radiation and function in a very regulated environment.
The design of the steam cycle impacts nuclear power plant efficiency; some use reheat cycles to increase thermal efficiency. Advances in materials and turbine design bring about ongoing improvements in steam turbine performance in atomic applications, improving the overall dependability and safety of nuclear power generation.
Gas-Fired Power Plants (Combined Cycle)
Combined-cycle power plants represent an important development in the application of steam turbines. To increase efficiency, these plants combine a steam turbine and a gas turbine. A gas turbine produces electricity in a combined-cycle system, and the waste heat from the gas turbine's exhaust is converted to steam, which powers a steam turbine to make even more electricity.
Among all power production technologies, combined cycle power plants have one of the greatest efficiency rates, frequently surpassing 60%. This is so because the energy that would otherwise be wasted as waste heat is efficiently captured and used by the steam turbine. Because they can swiftly ramp up or down in response to variations in the demand for electricity, combined cycle plants are also more adaptable than conventional power plants.
Natural gas has become a more appealing alternative for power generation due to the use of steam turbines in combined cycle facilities, especially in nations seeking to lessen their dependency on coal and cut carbon emissions. Combined cycle plants are an essential part of the contemporary energy mix since they may combine gas and steam turbines in a single plant, increasing efficiency and reducing environmental impact.
Geothermal Power Plants
Steam turbines are essential to producing electricity in geothermal power plants, which use the Earth's natural heat. Turbines in these facilities are powered by steam drawn from subterranean reservoirs. Because corrosive gases and minerals are frequently present in geothermal steam, turbine design and operation face particular difficulties.
The temperature and pressure of the geothermal steam determine the efficiency of geothermal power plants. Resources with higher temperatures can employ more effective steam cycles, such as those found in fossil fuel plants. Turbines that can manage a greater range of steam quality are necessary for geothermal plants, which normally operate at lower pressures.
Because geothermal resources are available around the clock, one of the main benefits of geothermal energy is its capacity to supply baseload power. Geothermal facilities' steam turbines need to be sturdy and dependable in order to run constantly with little downtime. Geothermal energy is becoming a more significant component of the renewable energy landscape as a result of advancements in turbine materials and designs that increase the durability and efficiency of geothermal turbines.
Concentrated Solar Power (CSP) Plants
Utilizing mirrors or lenses, Concentrated Solar Power (CSP) plants direct sunlight onto a receiver, which uses it to heat a fluid and create steam. Subsequently, this steam powers a turbine to produce energy. Because thermal storage devices store heat for later use, CSP is unusual among renewable energy sources in that it can generate electricity even when the sun isn't shining.
Because the amount of sunshine can change throughout the day, the steam turbines used in CSP facilities are made to run on fluctuating steam inputs. To match the amount of solar energy available, the turbines must be able to start and stop swiftly and effectively. Steam turbines with sophisticated blade designs and materials that can tolerate the thermal cycling brought on by sporadic solar input are frequently used in CSP systems.
One of the major advancements in CSP is the incorporation of molten salt thermal storage, which enables the plant to store heat during the day and use it to produce steam at night or during overcast conditions. Particularly in areas with high solar irradiation, CSP with steam turbines is a useful addition to the renewable energy mix because of its capacity to deliver dispatchable power.
Efficiency Considerations in Steam Turbine Power Generation
Since efficiency affects how well fuel or energy resources are transformed into electricity, it is a crucial component in steam turbine power generation. Several factors, such as operational tactics, technology developments, and thermodynamic principles, influence steam turbine efficiency.
Thermodynamic Efficiency
Thermodynamic principles, especially the Rankine cycle, the fundamental cycle utilized in steam power plants, have a significant influence on a steam turbine's efficiency. Isentropic Compression, isobaric heat addition, isentropic expansion, and isobaric heat rejection are the four primary processes that make up the Rankine cycle. There are various ways to increase this cycle's efficiency:
Superheating and Reheating: By lowering the steam's moisture content and increasing the amount of energy that can be recovered, superheating—the process of raising the steam's temperature before it enters the turbine—or reheating it in between turbine stages can greatly increase efficiency.
Increased Pressure Ratios: By running the turbine at greater pressures, more energy can be recovered from the steam, increasing cycle efficiency overall. The highest efficiency levels in contemporary power plants are found in supercritical and ultra-supercritical steam settings, where steam is produced at pressures higher than the critical point.
Regenerative Feedwater Heating: By using the steam from the turbine's intermediate stages to warm the feedwater before it enters the boiler, less fuel is used to generate steam, increasing the power plant's overall efficiency.
Technological Advances
Developments in steam turbine technology have significantly increased efficiency. Thanks to advancements in blade design, materials, and manufacturing processes, turbines can now function at higher temperatures and pressures, increasing the efficiency of energy conversion.
Advanced Blade Designs: Turbine blade efficiency is greatly influenced by their design. Modern blades are aerodynamically tuned to minimize losses from friction and turbulence. By utilizing computational fluid dynamics (CFD), engineers can create blades that optimize steam energy extraction.
High-Performance Materials: Steam turbines can now run at greater temperatures without losing structural integrity because of the development of cutting-edge materials like ceramic matrix composites and nickel-based superalloys. By preventing creep, corrosion, and thermal fatigue, these materials enable longer-lasting and more effective turbine operation.
Precision manufacturing and 3D printing: Additive manufacturing technologies, including 3D printing, have made it possible to produce turbine parts with intricate geometries that are efficiency-optimized. Turbine component uniformity and dependability are increased, and material waste is decreased, thanks to precision manufacturing procedures.
Optimizing the efficiency of steam turbines also heavily relies on operational tactics. Power plant operators can optimize steam turbine performance by carefully controlling operating parameters and load profiles.
Optimization of Load: Steam turbines function best when they are running at or close to their design capacity. However, electricity plants frequently encounter fluctuating demand throughout the day. By managing the turbine's load, operators can sustain high efficiency even during times of reduced demand. Strategies like load matching and peak shaving are used to ensure turbines run within their ideal range.
Real-Time Monitoring and Control: Thanks to sophisticated monitoring and control systems, operators of contemporary steam turbines can modify operational parameters in real-time. These systems track performance parameters, including steam temperature, pressure, and flow rate, using sensors and data analytics. By consistently tweaking these parameters, operators can increase productivity and stop problems before they cause performance losses.
Maintenance and Dependability: Regular maintenance is necessary to keep steam turbines operating efficiently. Predictive maintenance helps reduce downtime and guarantees that turbines continue to run at their best efficiency by using data analytics to identify when components are likely to fail. An efficient maintenance plan must include vibration analysis, blade inspection, and proper lubrication.
Environmental Impact and Mitigation Strategies
Although steam turbines are essential for producing electricity, they also pose a threat to the environment, especially when they are run on fossil fuels. Understanding and reducing these effects is crucial for steam turbines to operate sustainably.
Greenhouse Gas Emissions
One major source of CO2 emissions is the burning of fossil fuels in steam turbines, especially in coal—and gas-fired power plants. Reducing the carbon footprint of steam turbine power generation is essential because these greenhouse gas emissions contribute to climate change and global warming.
Carbon capture and storage, or CCS, absorbs CO2 emissions from power stations and stores them underground in geological formations. When combined with steam turbines, CCS can drastically lower the carbon emissions of fossil fuel-based power generation. Even though CCS adoption is still in its infancy, research and development efforts are being made to increase its scalability and cost-effectiveness.
Switch to Low-Carbon Fuels: Another way to cut greenhouse gas emissions is to switch from coal to lower-carbon fuels, like natural gas, or even carbon-neutral fuels, like biomass. Compared to conventional coal-fired power plants, combined-cycle power plants, which use both gas and steam engines, offer greater efficiency and reduced emissions.
Air and Water Pollution
Steam turbines that burn fossil fuels release CO2 along with other air pollutants like sulfur dioxide (SO2), nitrogen oxides (NOx), and particulate particles. These contaminants cause smog, acid rain, and respiratory issues in people.
Emission Control Technologies: To lower SO2 and NOx emissions from power plants, technologies like selective catalytic reduction (SCR) and flue gas desulfurization (FGD) are employed. Baghouse filters and electrostatic precipitators are two methods for controlling particulate pollution. These innovations lessen the negative effects of steam turbine air pollution on the environment.
Water Use and Thermal Pollution: Because steam turbines need a lot of water to cool, they may affect nearby water supplies. Aquatic ecosystems may also be impacted by thermal pollution, which is the release of heated water back into the environment. Power plants are increasingly using closed-loop cooling systems, which decrease water withdrawal and reduce thermal discharge, to address these problems. Particularly in areas with limited water supplies, dry cooling systems—which use air rather than water—are also being used.
Renewable Energy Integration
Integrating steam turbines with renewable energy sources can lessen the environmental impact of electricity generation. It is feasible to generate electricity with a reduced carbon footprint by utilizing steam turbines in combination with renewable energy technologies, including biomass, geothermal, and concentrated solar power (CSP).
Biomass Power Generation: Biomass power plants generate steam that powers turbines by using organic materials, including garbage, wood, and agricultural residues. Because the CO2 absorbed during biomass growth balances the CO2 released during combustion, biomass is regarded as carbon-neutral. A sustainable substitute for fossil fuels, steam turbines are essential in turning biomass energy into electrical power.
Geothermal and Solar Thermal: CSP facilities employ concentrated sunlight to create steam, whereas geothermal power plants use the Earth's natural heat. In both technologies, steam turbines transform thermal energy into electrical power. These renewable energy sources are appealing choices for environmentally friendly power generation since they emit few or no greenhouse gases.
Future Trends and Innovations in Steam Turbine Power Generation
Emerging trends and technology influence the direction of power production, so the steam turbine sector is always changing. In an evolving energy market, these advances aim to increase steam turbines' flexibility, efficiency, and environmental impact.
Decarbonization Initiatives
As the globe decarbonizes, steam turbines are being modified to run on low-carbon and carbon-neutral fuels. Hydrogen, in particular, is promising as a steam turbine fuel.
Hydrogen-Fueled Steam Turbines: Hydrogen is a carbon-free fuel that may be created by electrolysis utilizing renewable energy. Developments are being made to develop steam turbines that run on hydrogen, either by itself or in conjunction with other fuels. Particularly when used in combination with renewable energy sources, hydrogen-fueled turbines have the potential to generate dependable, low-carbon electricity.
Hybrid Energy Systems: Hybrid energy systems combine conventional power generation with renewable energy sources, and they increasingly include steam turbines. These devices can lower carbon emissions while supplying power continuously. A hybrid system might combine solar or wind energy with a natural gas-fired steam turbine, which would provide backup power in the event that renewable energy sources are sporadic.
Digitalization and Smart Grids
Steam turbines are operating more effectively, dependably, and responsively to grid demands thanks to digital technologies.
Artificial Intelligence and Machine Learning: AI and machine learning are being utilized to enhance turbine operations by evaluating data from sensors and control systems. By modifying operating parameters in real-time, these technologies can enhance efficiency, optimize load distribution, and forecast maintenance requirements. Additionally, AI-driven analytics are assisting in the discovery of patterns and trends that may improve turbine performance and decision-making.
Digital Twins: The idea of a digital twin—a computerized representation of a steam turbine that operates concurrently with the real machine—is gaining traction in the sector. With the help of digital twins, operators may simulate various scenarios, optimize operations, and keep an eye on turbine performance in real time without endangering the actual turbine. This technology is especially useful for anticipating and averting problems before they arise, which lowers maintenance expenses and downtime.
Integration with the Smart Grid: Steam turbines are being incorporated into smart grid systems, which provide increased power distribution and generation flexibility and efficiency. Steam turbines can react swiftly to variations in the demand for energy thanks to sophisticated control systems and real-time monitoring, which helps to maintain grid balance and avoid blackouts. Combining steam turbines with energy storage devices, such as batteries, improves grid stability and makes it possible to use renewable energy sources more effectively.
Research and Development
The goal of ongoing research and development (R&D) is to advance steam turbine technology, fulfil changing energy market demands, and tackle environmental issues.
High-Efficiency Steam Cycles: Supercritical and ultra-supercritical steam cycles, which run at greater temperatures and pressures than traditional cycles, are being developed primarily through research and development—higher thermal efficiencies provided by these sophisticated cycles lower emissions and fuel consumption. In order to increase their viability for broad adoption, researchers are investigating novel materials and designs that can endure the harsh conditions of these cycles.
Carbon Capture Integration: One of the main areas of research focused on lowering CO2 emissions from fossil fuel-based power generation is the integration of carbon capture and storage (CCS) technology with steam turbines. The goal of ongoing research and development is to increase CCS's effectiveness and affordability so that it may be implemented on a big scale.
Advanced Materials and Coatings: To increase the robustness and efficiency of steam turbines, new materials and coatings that can resist high temperatures and corrosive environments must be developed. The development of sophisticated coatings, including anti-corrosion and thermal barrier coatings, is extending the lifespan of turbine parts and lowering maintenance expenses.
Conclusion
For more than a century, steam turbines have been a vital component of power generation, and their function constantly alters in response to shifting energy demands and environmental issues. This thorough review of steam turbine power generation emphasizes the adaptability, effectiveness, and sustainability of steam turbines in a variety of applications.
Steam turbines are essential for generating dependable and effective electricity from nuclear and coal-fired power plants and renewable energy sources such as concentrated solar and geothermal. Supercritical steam cycles, sophisticated blade designs, and digitalization are only a few examples of technological developments that have greatly enhanced the efficiency and environmental friendliness of steam turbines.
Steam turbines will be crucial to decarbonization efforts as the world moves toward a low-carbon economy. Steam turbines are being modified to satisfy the needs of a more sustainable energy future in several ways, including the incorporation of hydrogen as a fuel, the use of carbon capture technology, and the creation of hybrid energy systems.
With continuous research and development propelling further advancements in efficiency, dependability, and environmental performance, steam turbines have a promising future. Steam turbines will become even more connected with smart grid systems as digital technologies like artificial intelligence (AI) and digital twins proliferate, increasing their adaptability and responsiveness to shifting energy demands.
To sum up, steam turbines will continue to be an essential part of the world's power generation for many years to come. They will continue to be crucial in the shift to a more robust and sustainable energy system because of their capacity to integrate with renewable energy sources and adjust to new technology.